Probing with switchable probe and measured value detection in the drive
Release Note
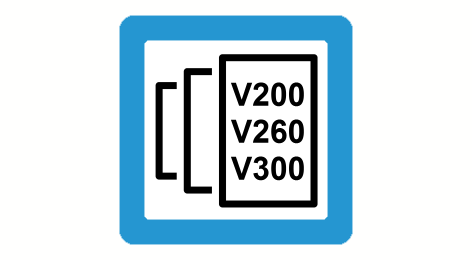
Function available as of V3.1.3080.05.
Basics
If a measuring probe is used that can be activated/deactivated when no measurement run is executed, the external measuring interface between the CNC and the PLC is used. (see Measure with external measuring hardware).
The CNC informs the PLC of the start and end of a measurement run so that the PLC can activate or deactivate the measuring hardware accordingly.
A possible application is the use of radio probes to save power. Since it may take a few seconds to enable the probe, it is recommended to prepare a measurement run using #MEAS PREPARE [AXNR = ..]. This allows the user to actuate the probe early so that there is no stopping at the start of the measurement run. The user is responsible for programming the #MEAS PREPARE command in good time. If a reset is executed between preparation and the actual measuring block, the probe is enabled as normal at the start of the measuring block.
Notice
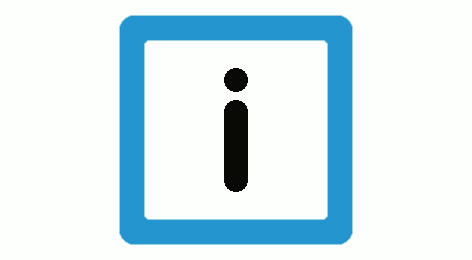
If homing is executed with one of the prepared axes before a measurement run is started, the preparation of all axes is reset. The same occurs when an axis prepared for a measurement run is exchanged from the channel. At the end of the program, all axes prepared for a measurement run are also reset.
CNC – PLC
The workflow from the CNC’s point of view is as follows:
The interface between the CNC and the PLC is used to signal the initialisation, the start and the end of a measurement run. The probe can then be prepared, enabled or disabled.
The CNC writes each task (HLI_EXT_LATCH_PREPARE_PROBE, HLI_EXT_LATCH_ENABLE_PROBE, HLI_EXT_LATCH_DISABLE_PROBE) with the required parameter number of the probing input and the relevant edge to the interface and sets please_rw = TRUE.
Notice
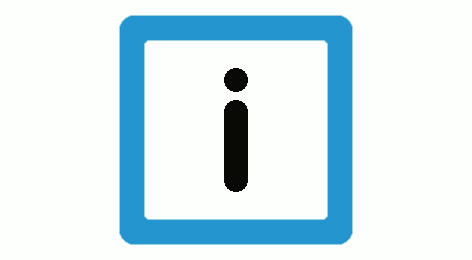
The interpolator does not move to the measuring block until the PLC acknowledges that probe preparation is completed.
The workflow from the PLC’s point of view is as follows:
After the task “HLI_EXT_LATCH_PREPARE_PROBE“ is received, please_rw is set to FALSE. When the probe is enabled, the PLC signals this to the CNC with done_w = TRUE.
Please note that the SPS must always acknowledge these tasks. At the start of the measuring block the task “HLI_EXT_LATCH_ENABLE_PROBE“ must be acknowledged. After the measurement run is completed, the CNC again informs the PLC with the task "HLI_EXT_LATCH_DISABLE_PROBE"; this task must again be acknowledged by the PLC.

Notice
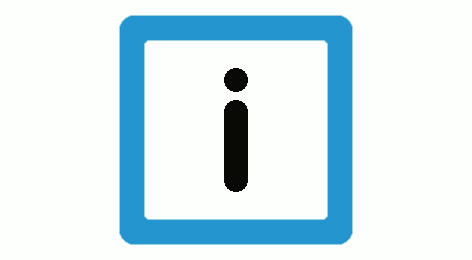
Before a new measurement run starts, the system waits until the PLC acknowledges the task “HLI_EXT_LATCH_DISABLE_PROBE“.
For more information on the interface structure, refer to the HLI documentation. (see Measure with external measuring hardware).
CNC – DRIVE
Depending on the drive type, the drive must be configured in the drive hardware as described in “Section: Measured value detection”.
Depending on the drive, the measured position is transmitted via the drive interface to the CNC.
Axis parameter
The following axis parameters are required for measuring with the CNC-PLC interface:
Select measurement method: | |
Number of the probing input used kenngr.measure.input 1 or 2 | |
Relevant measuring edge: kenngr.measure.edge POS or NEG |
Alternatively, the measuring interface can also be enabled in the NC program by the #MEAS command (see [PROG//Extended programming]).