Introduction
Extensive data volumes are exchanged between the CNC and the PLC. For example, this comprises
- Commands from the NC program of the CNC to the PLC (e.g. technology commands, such as M, S, T and H commands etc.).
- Acknowledgements of technology commands by the PLC.
- Display data of the CNC (e.g. current axis positions, current and programmed path velocity etc.).
- Jobs from the PLC to the CNC (e.g. mode switchover, set feedhold etc.).
- Jobs from the GUI to the CNC which can be verified and, if applicable, denied by the PLC (e.g. mode switchover, set feedhold etc.).
The interface between CNC and PLC is outlined in the overview diagram below.
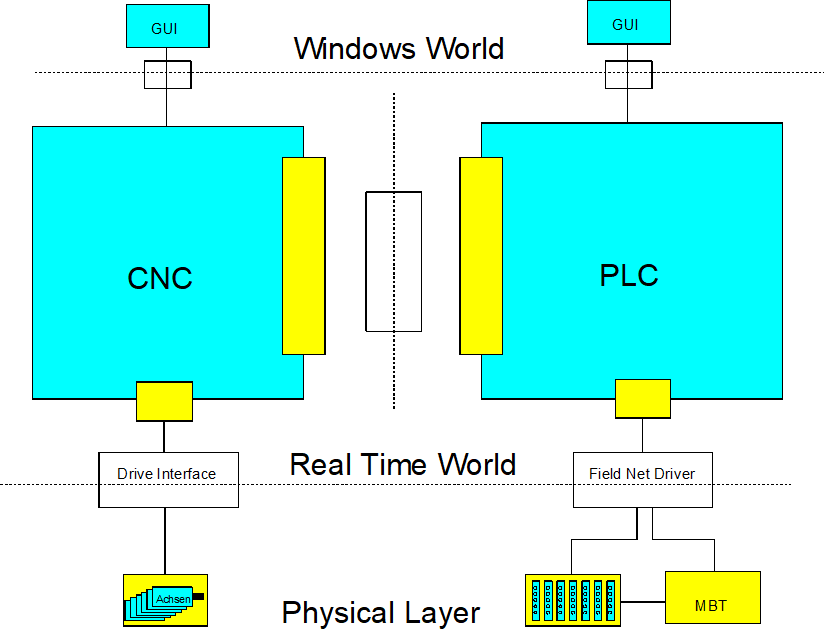
This documentation describes the structure of this interface between CNC and PLC referred to below as High-Level Interface (HLI for short).
The term “High-Level Interface”, in this context, refers to the structure of the interface with complex data structures and handshake variables. This has to be seen in contrast to a data interface, which us considered to be at a low level of abstraction (Low-Level Interface).