Operation with and without PLC
Machine start-up can also be performed with partially implemented PLC functionality. The CNC-side driver of the HLI therefore contains mechanisms for the internal simulation of interactions between PLC and CNC.
Example:
The axis should be run in with a rudimentary PLC. The PLC sets only the Axis Enables; other functions are not yet implemented in the PLC.
In order to switch operation modes or perform a reset anyway, the HLI driver simulates the required acknowledgements of the PLC so that the required action can still be performed.
In order to achieve this behaviour and still ensure reliable operation, the PLC issues a corresponding information item to the CNC for each function covered by the PLC, a so-called “present” marker. "Present" means that the PLC claims control of the interface and sends the required acknowledgements.
The PLC must then inform the CNC that it exists, once globally in the HLI. In addition all control commands are enabled individually.
This means that three scenarios are conceivable:
- CNC without PLC
- CNC with PLC which does not use all elements of the HLI
- CNC with PLC which uses all elements of the HLI
The housekeeping sections of each channel or each axis has this “present” element by which the PLC assumes responsibility for this interface.
In addition, each housekeeping unit of a control command, i.e. the control unit, contains an element which the PLC uses to inform the CNC that it supports this command. The enable_w element means at the same time that, if the corresponding command is issued via the GUI, it is routed via the PLC and reaches the CNC from there. The CNC can then no longer distinguish whether a command arrives from the PLC or the GUI.
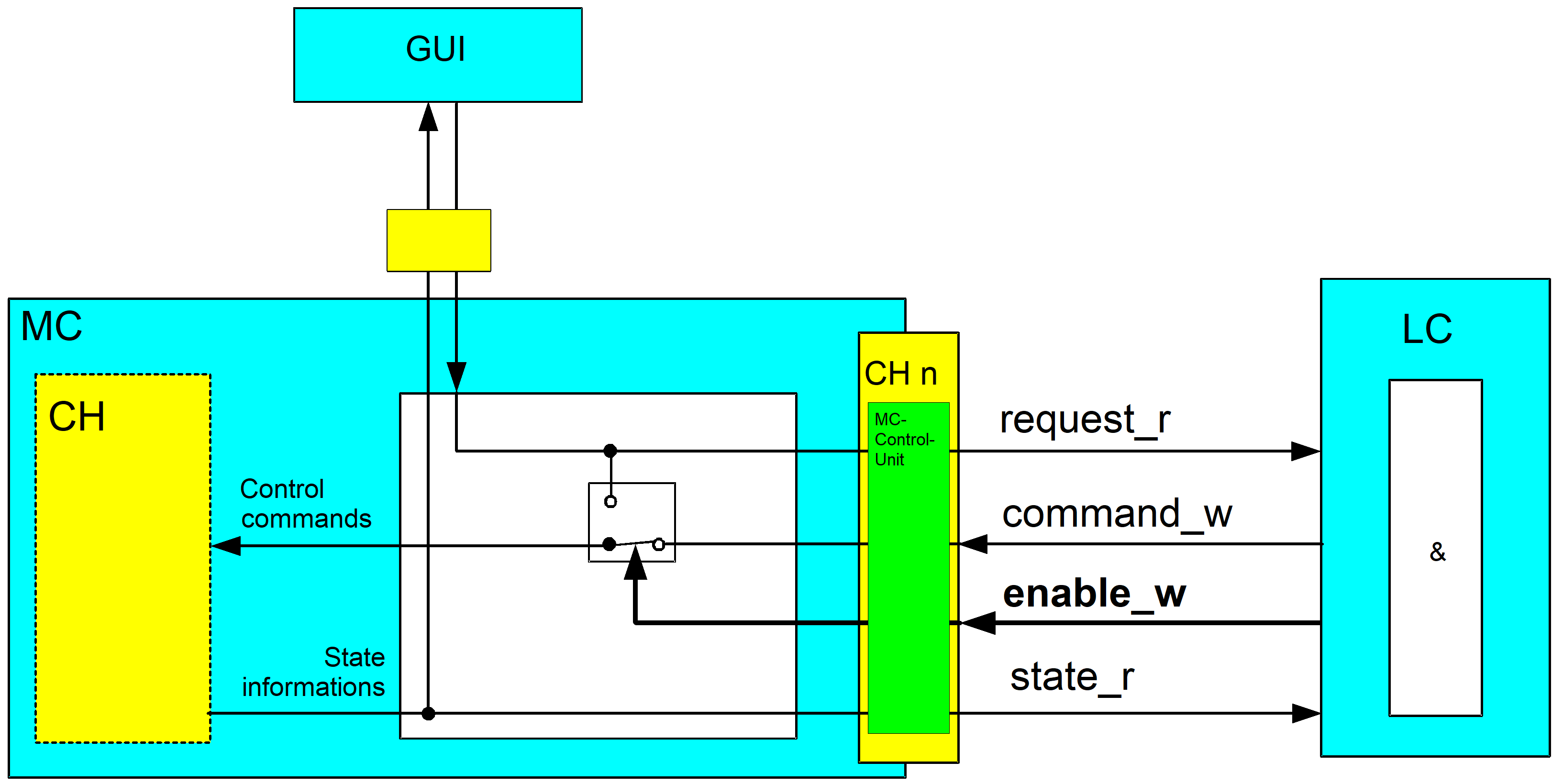
The connection of the GUI via the CNC is not absolutely necessary. Similarly, an interface can communicate directly with the PLC and the additionally provided communication channel GUI -> CNC -> PLC is not used in such cases.