Axis errors from the motion controller
The motion controller uses the axis-specific interfaces of the HLI to provide messages about an axis for the PLC. The information is exchanged via a data structure of the type HLI_ERROR_SATZ.
TYPE
HLI_ERROR_SATZ :
STRUCT
error_id : UDINT; (*Error number*)
(*System time when error occurs*)
fb_zeitangabe: HLI_FB_ZEITANGABE;
bf_type : WORD; (*BF type*)
behebungs_klasse: WORD; (*Error rectification class*)
reaktions_klasse: WORD; (*Error response class*)
reserved : WORD;
END_STRUCT;
END_TYPE
Instances of the FB MCV_Axis check this axis-specific area in every PLC cycle because these are instanced in the MCV_P1_PLATFORM program and must be integrated first in the PLC task in conformity with the explanations in Section 1.2.3.3 of this program description. The MCV_Axis extracts every newly occurring message and transfers it to the AXIS_REF structure of the assigned axis, which contains one field for six data structures of the type HLI_ERROR_SATZ.
If a message has been classified as an error, the MCV_Axis instance sets the current state of the axis state diagram (AXSD) to ERROR_STOP.´
Notice
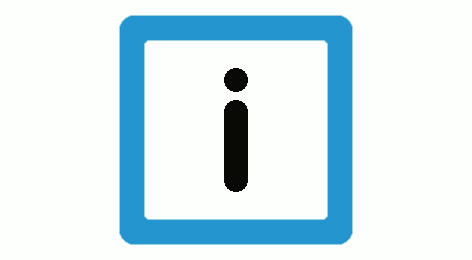
Error messages are all those messages for which the value of the variable is behebungs_klasse > 0.
If the value of behebungs_klasse = 0, the message is a warning.
The ERROR_STOP state is detected by the other PLCopen FB instances to which the same axis is assigned. Consequently, they set their "Error“ output variable to TRUE and the value 1 (ERR_PLC_AX_MC, see P-ERR-40001) is indicated at the “ErrorID” output variable.