Tool geometry compensation (D)
Tool geometries are compensated for length, radius and axis offset. The corresponding compensation data for tool geometry are provided either by:
tool data lists containing data records for each tool and loaded at controller start-up (see [TOOL]), or an external tool management system.
Tool compensation data
Tool compensation data is selected using the D word or is selected automatically by the T word (P-CHAN-00014) if this is parameterised.
Syntax: | ||
D.. | Selecting tool compensation with number of the compensation data block. Positive integer. | modal |
The D word defines a tool data block that contains the following values:
- Tool length (perpendicular to main plane)
- Tool radius (in the main plane)
- Axis offset coordinates (in all axis directions)
- Measuring unit of the numerical statements (mm/inch)
- Tool validity code
- Tool dynamic data
Attention
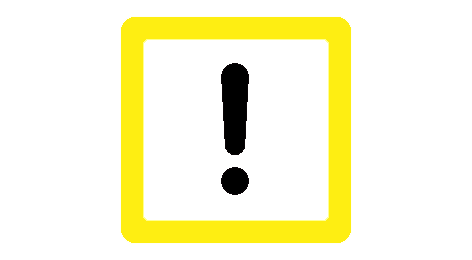
The time when the tool compensation data for the tool length (perpendicular to the main plane) and the axis offset coordinate (in the axis directions) become effective is programmed by the channel parameter P-CHAN-00100. The lines below must also be noted:
A distinction is made between 2 modes:
The compensating movement is executed directly with the D word without specifying a path preparatory function.
For safety reasons, the controller only executes the compensating movement at the next absolute motion block in the corresponding axis (default mode).
In G91 mode, the following applies to the inclusion of tool compensation data:
The programming of...
N10 D16
N20 G0 X0 G91
... may not cause any movement of the X axis (corresponds to relative movement about 0). In this case, tool compensation data for this axis only acts if the next motion information is programmed in absolute coordinates (G90).
Please note for both modes together: The tool radius is transferred to the tool radius compensation and influences the equidistant calculation. The compensating movement always take place combined with a path preparatory function.
The rules for execution of the compensating movement also apply to deselection of tool compensation.
Syntax: | ||
D00 | Deselect tool compensation | modal |