Compensating axis position errors
Axis position error
On a real machine, axes are not normally in the assumed ideal position.
For example, the X axis may have a disrupted orientation vector, i.e. may not point towards (1, 0, 0) in the machine coordinate system but towards (0.99953, 0.0002, -0.0004). This value is obtainable by a compensation calculation in a measurement cycle, for example.
These deviations can be mapped in the kinematics. Instead of
# Define X axis
kinematik[91].axis[0].orientation[0] 1
kinematik[91].axis[0].orientation[1] 0
kinematik[91].axis[0].orientation[2] 0
…
set the following values:
# Define X axis
kinematik[91].axis[0].orientation[0] 0.99953
kinematik[91].axis[0].orientation[1] 0.0002
kinematik[91].axis[0].orientation[2] -0.0004
…
Compensating axis position errors
Generally:
- Errors in linear axes can be compensated by correcting the Cartesian axis values.
- Errors in rotary axes can be compensated by correcting the Cartesian and rotary axis values.
Correcting axis values
When axis values are calculated, the kinematics considers and compensates for axis position errors. It determines axis values that then initiate correct tool positioning and orientation on the defective machine.
Attention
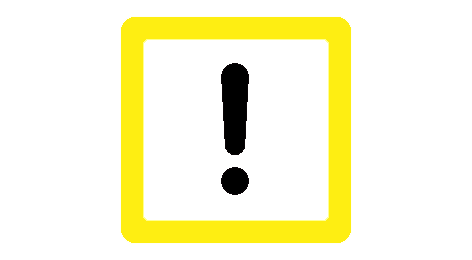
Exception:
In RTCP mode the kinematics adopts the programmed axis angles. Axis angle correction is therefore not possible.
However, Cartesian axis values are still corrected.