Programming
Syntax, definition of a gantry coupling
The #SET AX LINK and #AX LINK NC commands are provided in extended syntax for the programmable gantry mode:
#SET AX LINK [ <coupling_group>, [ <slave>=<master>,G [,<limit_1>, limit_2>] ] {, [ <slave>=<master>,G [,<limit_1>, limit_2>] ] } ] or alternatively #AX LINK [NBR] [ <coupling_group>, [ <slave>=<master>,G [,<limit_1>, limit_2>] ] {, [ <slave>=<master>,G [,<limit_1>, limit_2>] ] } ] |
<coupling_group> | Number of the coupling group 1 ... [Max. number of coupling groups(1) -1] , positive integer. |
<Slave> | Designation or logical axis number of the slave axis of the coupling pair i |
<Master> | Designation or logical axis number of the master axis of the coupling pair i Max. number of coupling pairs (2) |
NBR | Evaluation can be changed from logical axes names to axes numbers with the logic switch NBR. The axis couplings must then be defined with logical axis numbers. The axes need not be present in NC channel. Their availability in NC channel is checked only at activation of the coupling group! |
G | Keyword for gantry coupling With a gantry coupling the position difference is checked between the actual positions of the coupled axes and the <limit_1> and <limit_2> positions in the specified limits. Any existing position offset is taken into account when gantry coupling is activated. |
With a gantry coupling the following values are used for two-stage monitoring of the permitted position difference between the gantry axes. Specified in [mm]. Positive real number: | |
<limit_1> | 1st monitoring limit: |
<limit_2> | 2nd monitoring limit: |
Notice
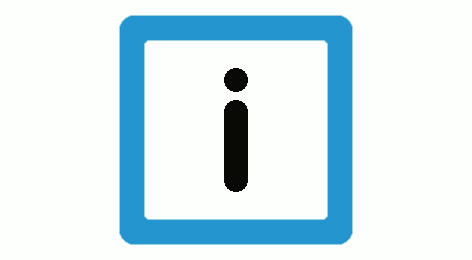
If the monitoring limits are not programmed, the defaults apply from the axis parameter data records P-AXIS-00072 and P-AXIS-00071 of the slave axis.
Handling and operating principle
- Gantry coupling takes place at precisely the positions where the axes are located at the time when coupling is selected. There is no need to specify an offset in the NC command because the offset is calculated internally in the position controller via the nominal positions.
- The dynamic data of the slave axis is taken into account in the contouring motion.
- If programmed accordingly (P-CHAN-00104/P-CHAN-00105), a coupling that is still active on RESET or at program end is implicitly restored for safety reasons the next time the program is started.