Controlled spindle
Functionality
For certain applications it may be sufficient to simply operate a spindle in purely speed-controlled mode by outputting a speed command value instead of operating it in a position-controlled loop.
Drive types
A speed-controlled spindle can be configured for drive types Terminal, Lightbus and EtherCAT/CANopen.
Principle of operation
For a speed-controlled spindle the speed command value of the interpolator is output directly to the axis and not the speed command value of the position controller.
The acknowledgement of speed commands to the spindle is derived from the following actual values depending on the actual value telegram configured:
- If an actual position value is configured, the actual speed is calculated from the actual position values. However, the encoder resolution must be specified in the axis parameter list.
- If a speed actual value is configured and not an actual position value, the speed actual value is used to acknowledge the speed.
- If neither an actual position value nor an actual speed value is configured (sensorless spindle), the speed acknowledgement is calculated from the internal speed command value. The speed is considered as reached when the internal speed command value calculated cycle by cycle is within the speed tolerance specified in the axis parameter list.
A sensorless spindle cannot be positioned. If an attempt to do this is made despite this, error message 70252 is output.
For the actual spindle speed to match the programmed spindle speed, the scaling factor must be correctly adjusted for the speed command value.
A speed-controlled spindle can be configured for drive types Terminal, Lightbus and EtherCAT/CANopen.
Notice
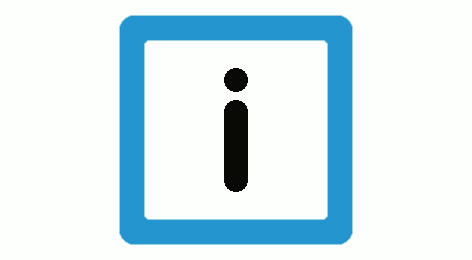
For terminal drives, offset voltages in the analogue input part of the drive controller may lead to a slow rotary spindle movement, even if a spindle speed of 0 is programmed.
This can be prevented by:
- Offset adjustment of the drive amplifier.
- Disabling the drive amplifier by the PLC at speed 0.