Specifying the workpiece surface (SET_POS, surface)
Calculating deviation
The deviation of the real workpiece surface from the specified command position (SET_POS) is determined in each cycle by the electronic probe. Deviation results from:
Deviation = motor encoder + sensor encoder - set position (SET_POS)
= actual workpiece surface position - set position (SET_POS)
To compensate for the workpiece surface deviation, the drive position is additionally moved by the calculated offset of the distance control:
Drive setpoint = programmed setpoint (PCS) + distance control offset
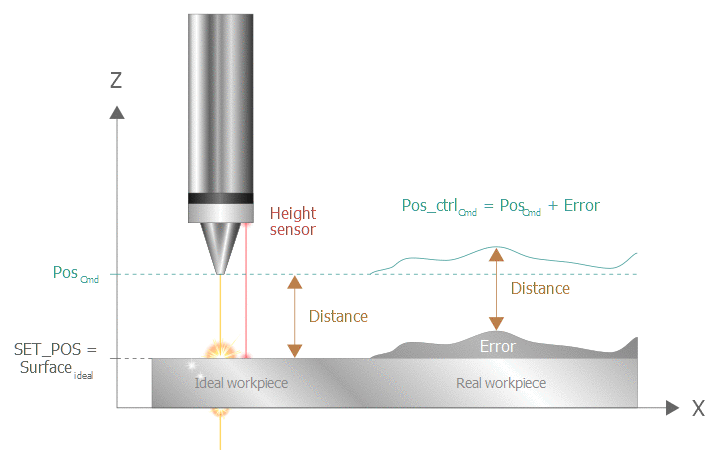
Selecting and deselecting via the NC program
The NC program activates and deactivates distance control and also freezes the current correction value. Example:
N10 Z[DIST_CTRL SET_POS=30] Set the position
Nxx Z[DIST_CTRL ON] Select
…
Nxx Z[DIST_CTRL OFF] Deselect
N999 M30
The complete CNC syntax is described in the Programming chapter.
Typical sequence
Typical sequence for activating distance control:
- The tool is replaced.
- X and Y axes move to machining position.
- Distance control is activated and the workpiece set position is set. The Z axis must then be located within the detection range of the distance sensor.
- Sensor or probe ring signals distance; distance control corrects height errors.
- Z axis is lowered.
- Distance control is active; thickness tolerances or position differences are compensated.
Deactivating distance control:
- Distance control is deactivated via the NC program
- Distance control is inactive; thickness tolerances or position differences are no longer compensated; and the current offset remains active until the next position request.
Operating principle
With distance control, deviations in the position of the workpiece surface (actual position) can be corrected with respect to a specified set position:
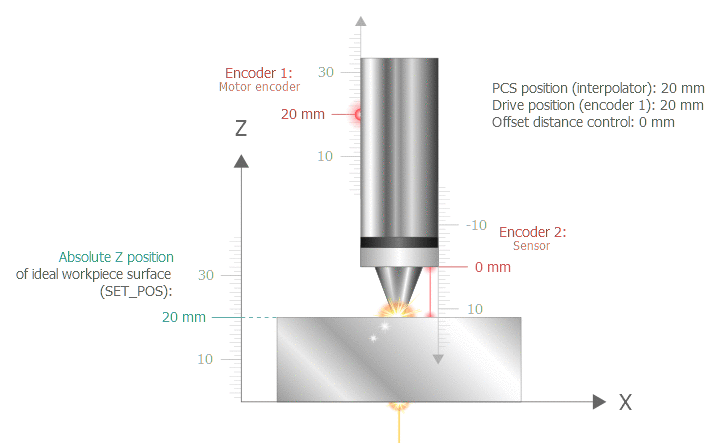
Deviation
A deviation from the ideal workpiece surface (e.g. with a thinner workpiece) is detected by the sensor (encoder 2):
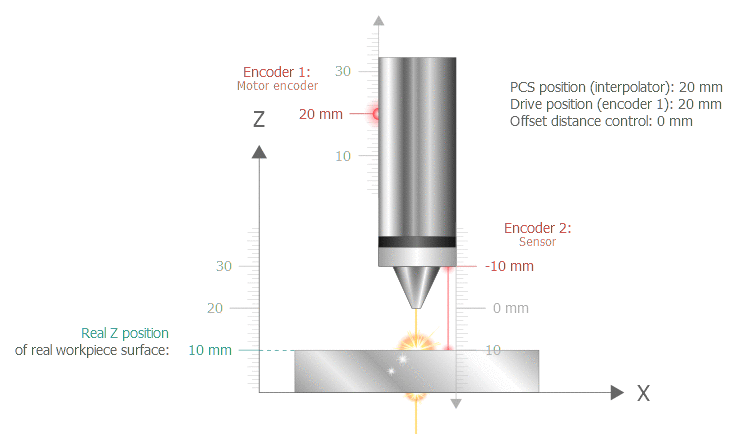
Offset compensation
After activation of distance control with SET_POS=20 mm (expected workpiece height), the offset is compensated by distance control. As a result, there is no need to adapt the NC program (PCS position). The NC program assumes a constant workpiece surface of Z=20 mm.
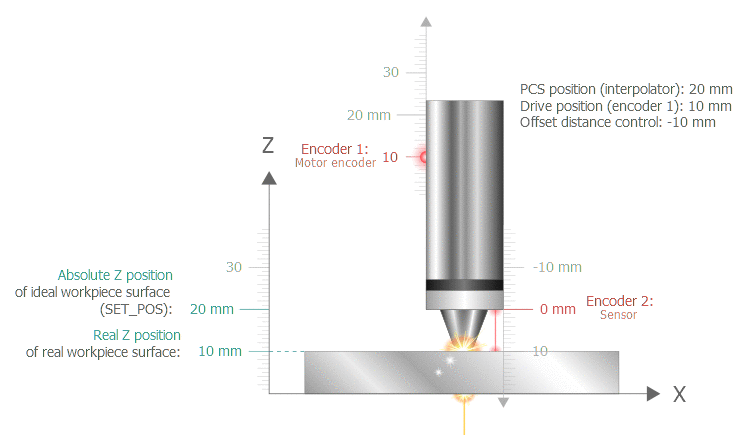
Notice
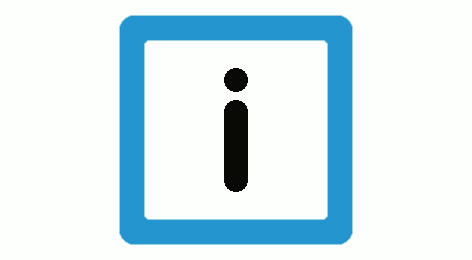
Distance control is automatically deactivated if an axis error or a CNC reset occurs.
At program end, distance control remains active.
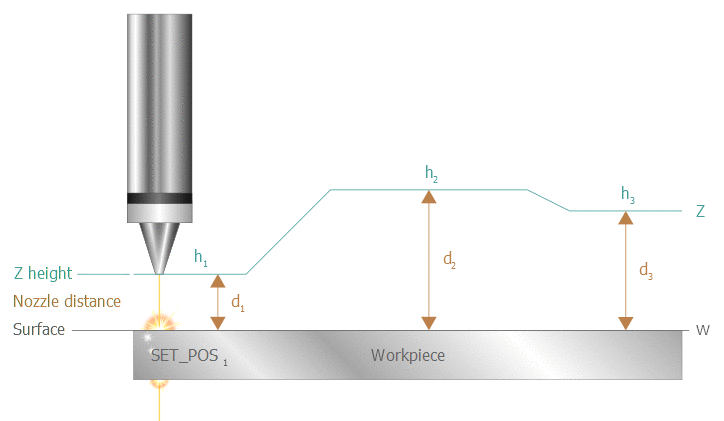
Height changes
Changes in the workpiece surface are compensated by distance control. The NC program therefore assumes a plane workpiece. Height changes in the workpiece surface can be defined by programming the axis. At Z=SET_POS the TCP tip touches the workpiece surface.