5-axis, one orientation axis in both workpiece and tool
Release Note
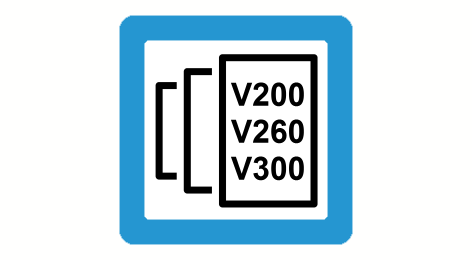
This functionality has been available since CNC Build V2.11.2807.20.
Round tube machining
These kinematics are intended for machine tools with 5 machine axes which are specialised for tube machining only.
This requires a configuration of 5 real machine axes and one virtual axis or one simulation axis. The machining orientation is defined by one rotation axis in the tool and one in the workpiece.
The TCP is positioned for tube machining with the X/Y axis above the top point of the tube. As opposed to 6-axis kinematics the TCP does not remain at the top point of the tube when there is a change in orientation but drifts along the surface of the cylinder. This must be considered to avoid collisions between the workpiece and the tool holder.
The path is programmed on the lateral surface by the axes U, Y and X, V. Orientation is programmed dependent on the existing kinematics.
- A-U or B-V structures are programmed directly using the assigned angle values A-B or B-A.
- When virtual axes CA are used for parametrisation, these angles are used for programming.
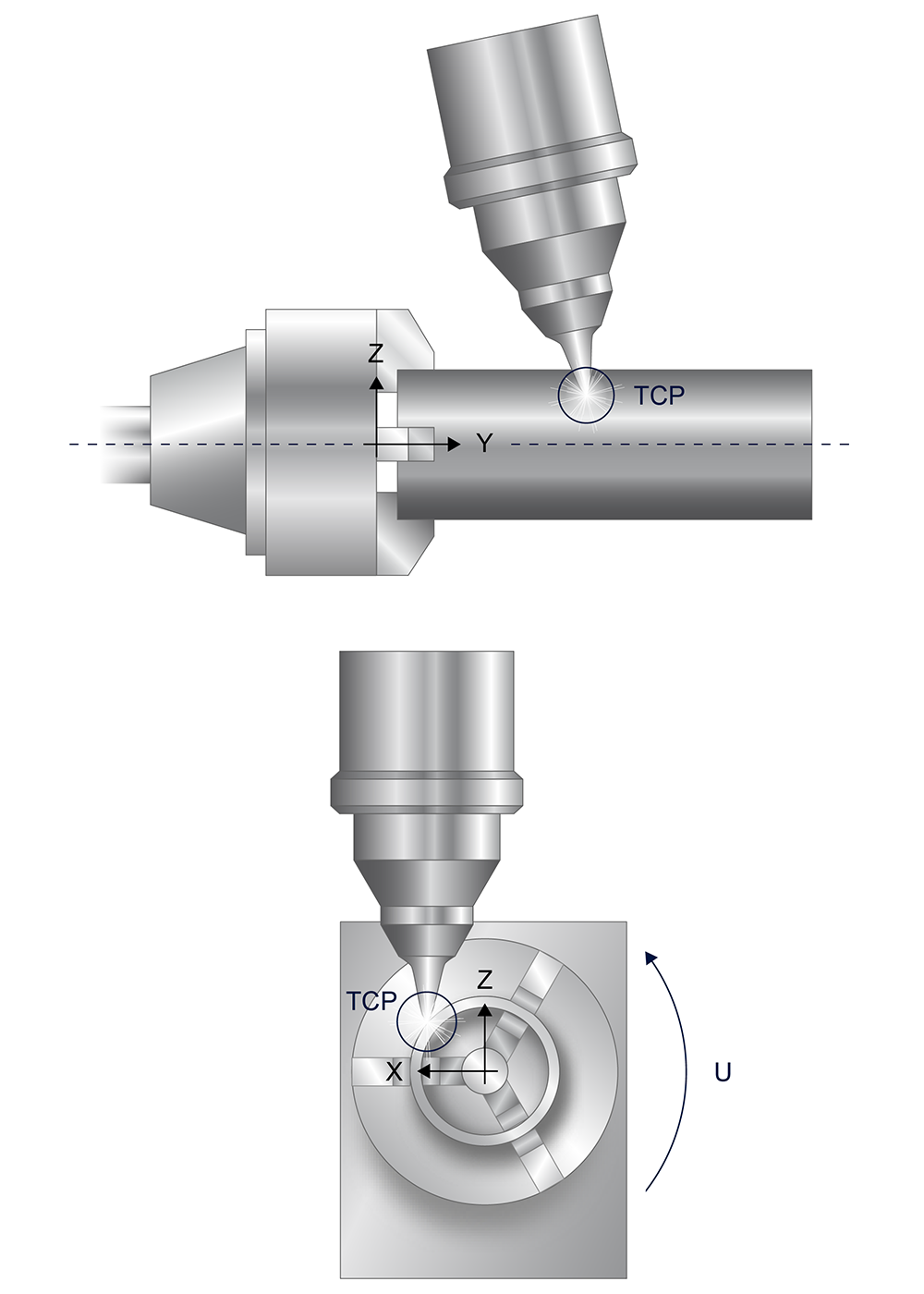