Polygonal tube, profiled tube (kinematic ID 79)
Parameters are defined under the ID 79 of the kinematic offsets (P-CHAN-00263 and P-CHAN-00094).
HD offset | param[i] | Description | Unit |
HD1 | 0 | Z offset tool fixing point - Tool carrier reference point | 1.0 E-4 mm |
HD2 | 1 | X offset tool fixing point - Tool carrier reference point | 1.0 E-4 mm |
HD3 | 2 | Y offset tool fixing point - Tool carrier reference point | 1.0 E-4 mm |
HD4 | 3 | Z offset of rotary axis U to machine zero point | 1.0 E-4 mm |
HD5 | 4 | X offset of rotary axis U to machine zero point | 1.0 E-4 mm |
HD6 | 5 | Y offset of rotary axis U to machine zero point | 1.0 E-4 mm |
HD7 | 6 | - |
|
HD8 | 7 | Angle offset of workpiece clamp position | 1.0 E-4° |
A modulo compensation is always executed for the U axis.
The general description is contained in the channel parameter list under P-CHAN-00263 and P-CHAN-00094.
When the rotary workpiece axis is in zero position, the clamped workpiece is normally not in the specified basic orientation where the workpiece axis is perpendicular to the profile section. The kinematic parameter HD8 considers the clamp position of the profiled tube. In this case, the workpiece must be oriented above the rotary axis so that a plane surface of the profile is perpendicular to the tool. In the current example the U axis is moved to -60°; the required offset setting is then +60°.
In the above figure, the lateral surface system is then obtained after the transformation is selected according to following parameters #CYL[EDGES=3 ROUNDING=5 LENGTH1=50]. The zero point of the lateral surface system is located in the middle of lateral plane 1; the PCS start position of the TCP is UPCS = +19mm.
In the following case the transformation should be activated on the lateral surface 2. The clamping position and kinematic parameter HD8 correspond to the above example. The U axis is positioned at 180° before the transformation is selected so that the tool is perpendicular to the required plane surface.
In the above figure, the lateral surface system is then obtained after transformation is selected according to the following parameters #CYL[EDGES=3 ROUNDING=5 LENGTH1=50]. The zero point of the lateral surface system is located in the middle of lateral plane 1; in the lateral surface system, it is located at the start position UPCS=145mm.
In this case the transformation should be activated on the profile rounding 12. The clamping position and kinematic parameter HD8 correspond to the above example. The lateral surface system is obtained after transformation is selected as shown in above figure. The system is located at the start position UPCS=136.94mm. The approach to the profile rounding at position UPCS=148.94mm is executed by positioning with the command #PTP ON.
Programing Example
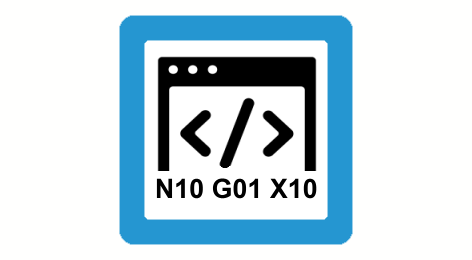
Polygonal tube, profiled tube (kinematic ID 79)
N30 ...
N40 G0 G90 X0 Y=20 U=0 Z50
N50 #CYL [EDGES=3, ROUNDING=5, LENGTH1=50]
N60 #PTP ON
N70 G0 G90 U148.94 Z40
N80 #PTP OFF
N90 Z0
N100 G01 U150 X5
...