Saving tool life parameters
Service life/service distance
When service life values are captured, the contact time (service life) and the distance covered by the tool during contact (service distance) must be calculated.
By default, only travel by motion blocks is considered. Positioning by rapid traverse has no effect on service life parameters.
The parameter P-CHAN-00255 is used to adapt service life data capture to a specific application, This then includes all motions and rapid traverse motions in service life data capture. At the same time, service life data capture can be suppressed by using the channel-specific Control commands of a channel control unit on the HLI to meet specific user requirements. This permits the complete adaptation of service life data capture to user requirements.
After the tool is exchanged, the interpolator displays the data: tool ID, contact time and contact distance.
Notice
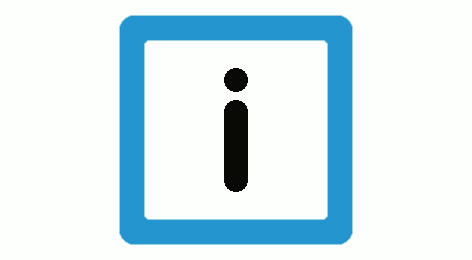
Service life is captured in [s]; service distance is captured in [mm].
Time of storage
The complete tool ID, service life and service distance are sent automatically by the CNC to the WZV (tool management system) every time a tool change is announced by the T command and if P-CHAN-00076 is set, By default, service life data is sent to the tool management system even if service distance/service life are set to the value 0. The parameter P-CHAN-00243 suppresses the transfer of service life data when it has the value 0.
After service life data is transferred, all parameters are set to 0 in the interpolator. This is followed by service life data capture for the tool that was just replaced.
Weighting
The NC program can change the weighting of service life values. The changeable factor is used to adapt service life data capture to tool use.
Weighting factors
The following 2 decoder variables are used to program the weighting factors for service life and service distance (access is not synchronous with real time):
Weighting of service life: V.TLM.TIME_FACT
Weighting of service distance: V.TLM.DIST_FACT
The variables are readable and writable. Both factors are 100% at program start. Both variables may be written in an NC block.
Example
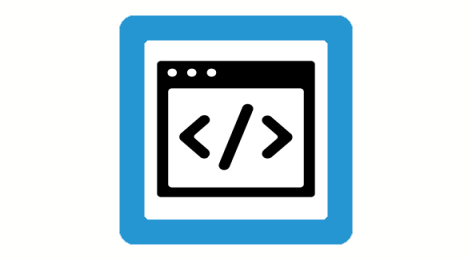
Saving service life parameters
A tool that is always in contact should be weighted with a factor of 100%. However, if material is only removed on half the motion path, a weighting factor of 0.5 may be included in the calculation.
The default value of the weighting factors for service time and service distance is 1.0.
Notice
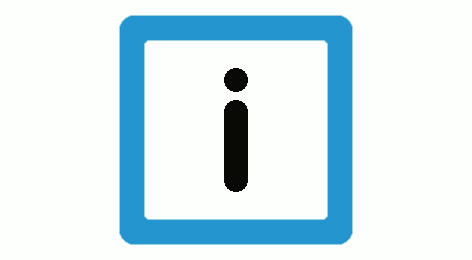
Capture conditions:
If the parameter P-CHAN-00255 is not set, all motion types are included in service life data calculation except for rapid traverses. For example, G01, G02, G03, spline interpolation and G63 are included in the service life data calculation.
If the parameter P-CHAN-00255 is set, all motion types are included in service life data calculation.
Service life data capture is stopped if the feed rate is 0.
The weighting factors are included in the calculation.
A distinction is not made between main and tracking axes for axes participating in the motion. The path feed rate is always used to add up the distance. If tracking axes are programmed on their own in the block, the path covered by the tracking axis is added to the service distance. If this is not desired, the programmer can correct it by specifying the weighting factors V.TLM.TIME_FACT/DIST_FACT = 0.
Active master/slave arrangements are not taken into account.
If a reset or program abort occurs, the last current values are also saved to the database of the tool management system.
If a tool is exchanged for the first time, i.e. the work spindle was previously empty and the current T number is equal to 0, no data is sent.