Description
Boundary condition
Basically a spindle can be operated position-controlled or speed-controlled. The operation mode is defined statically in most cases, whereby all the parameters required for each operation mode must be configured in the drive telegram for SERCOS and CANopen drives.
If a modulo transition takes place in the drive positions in position-controlled mode (position control in the drive), the maximum speed is limited to 180° per tracing cycle for spindles. Otherwise, the drive controller cannot determine the rotation direction from the specified path change. For example, for a tracing cycle of 2 ms, this results in a maximum speed of 15,000 rpm.
When a spindle drive is operated at current limit, it may result in an excessive position lag at high speeds, causing error messages in the drive and/or the CNC. This may make it necessary to change to controlled operation (no position control) at high speeds and to only operate the spindle position-controlled for positioning movements.
Functionality
To permit higher speeds, the spindle is operated
- speed-controlled with speed-only programming and
- position-controlled when a position is specified.
A change between the two operation modes can take place automatically during the movement.
- With CNC position-controlled drive, an operation mode changeover takes place internally in the controller.
- With speed-only programming, the position control loop is opened automatically and a speed command value is sent to the drive.
Notice
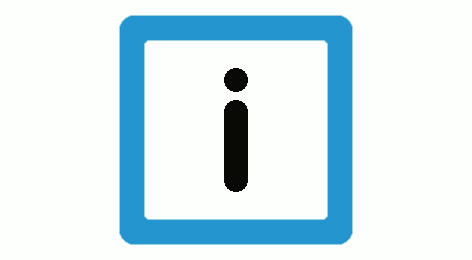
If position control takes place in the drive, the changeover between position and speed control is always supported by the drive.
Automatic changeover by the CNC with position control in the drive is only available for SERCOS and CANopen drives.
The drive needs no special requirements for automatic changeover for drives with position control in the CNC:
Programing Example
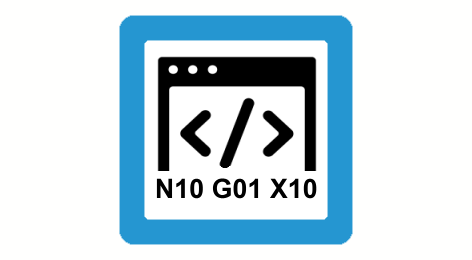
Changeover of operation mode
%spindle-position
N30 S200 M4
N40 M19 S.POS=180 S1000 M4
N50 S200 M3
N60 M19 S.POS=180 S1000 M4
N70 S200 M4
N80 M19 S.POS=180 S1000 M3
M30