Properties
Changeover to speed control
If a speed (S word) is programmed with M3 or M4 and it is higher than the specified changeover parameter, the system changes over automatically to speed control.
Switch back to position control
A switch-back to position control takes place under the following conditions:
- Positioning was programmed with M19.
- A CNC reset was triggered.
- A spindle axis was issued from the spindle interpolator (NC command S[PUTAX]).
- Homing was started (G74).
Notice
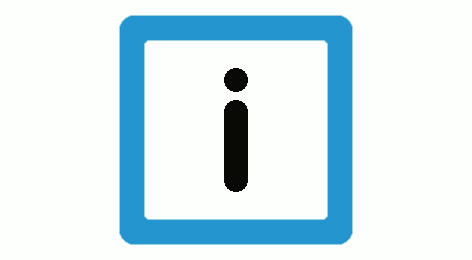
If a previous speed programming was changed over to speed control, no switch-back to position control takes place if an additional speed below the switch-back speed is programmed.
Effect of switch-back speed
The command position is not considered during speed control. When a changeover occur to position control, the CNC determines the theoretical command position of the next cycle using:
- the current speed
- the Kv factor (of the drive or the controller position control) and
- the bus run time
The axis can then be switched back to position control without standstill.
The switch-back speed indicates the speed at which switch-back to position control may take place.
Notice
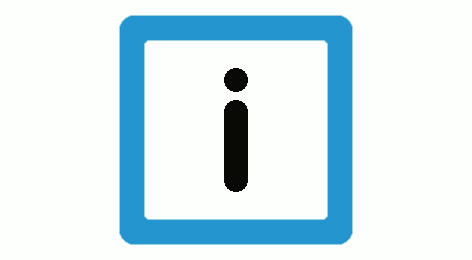
Since the actual speed may fluctuate slightly, especially at high speeds, a slight jerk may occur in the drive at high speeds on switch-back to position control.
For this reason, do not select a switch-back speed that is too high.
Programing Example
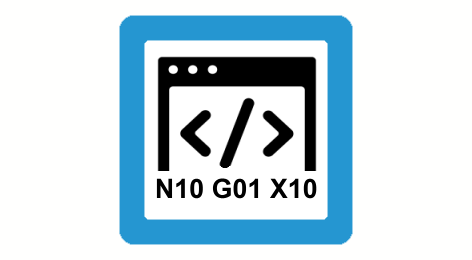
Effect of switch-back speed
%spindle-position
N10 M3 S1000
N20 M19 S.POS=180 M4 S50
M30
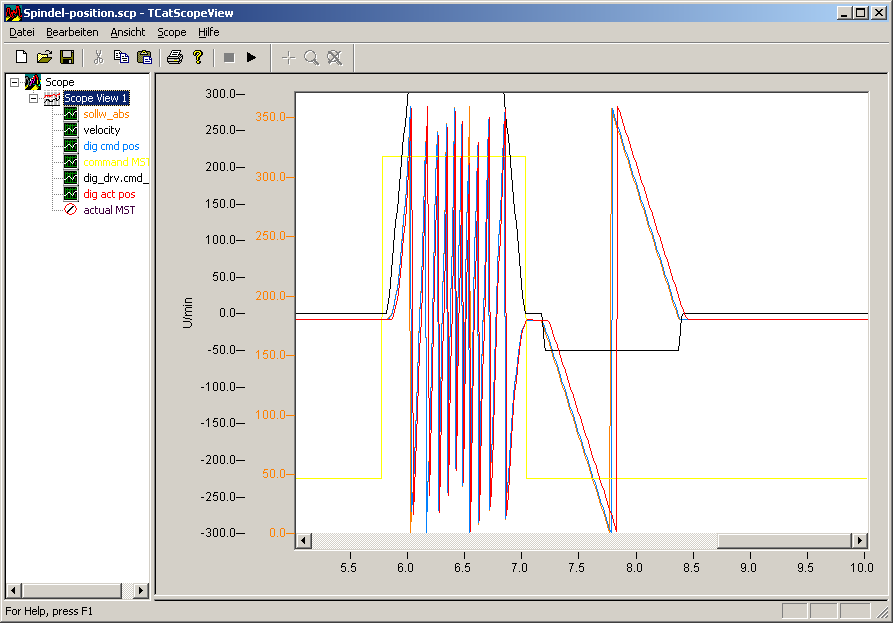
Programing Example
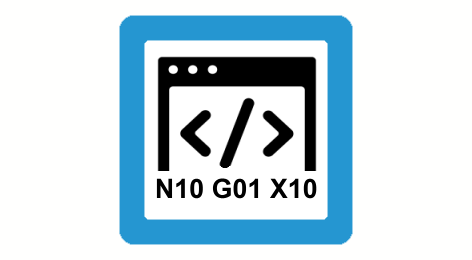
Special case
If the positioning speed is above the changeover speed with M19, positioning still takes place in position-controlled mode.
Depending on the distance traversed, it is therefore possible to traverse above the changeover speed for a short time in position-controlled mode.
%spindle-position
(antr.sai_op_mode_change.v_velocity_control_on 1200000
( -> 200 rpm
(antr.sai_op_mode_change.v_position_control_on 600000
( -> 100 rpm
N10 M4 S1000
N20 M19 S.POS=180 M4 S500
M30
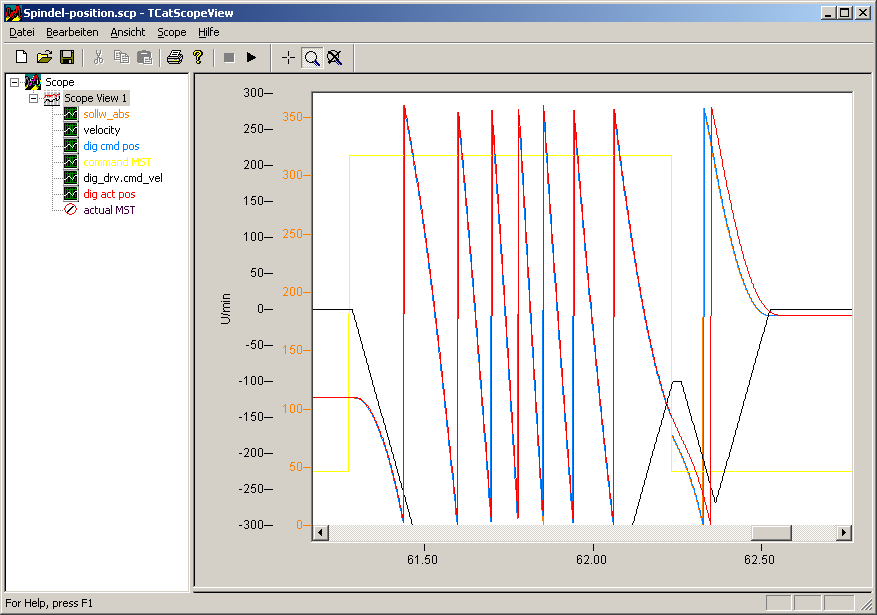