Axis clamping and monitoring (#CLAMP MONITORING)
To ensure high quality and accuracy in a machining process (milling, turning, erosion machining, etc.), the tool-carrying axis can by physically fixed by the drive brake. Mechanical axis clamping is commanded by synchronised M/H functions in the NC program and enabled in the PLC. This ensures that an axis is clamped before the next motion block is executed.
The status ‘clamped axis’ is effective at axis driver level and remains valid cross-channel until it is deselected, even with axis exchange operations.
While an axis is clamped, neither the interpolator nor an additional interface can command it to drive by command values. The monitor required here is enabled and disabled by the following NC command. If a clamped axis is to be moved, the error message P-ERR-70525:is output and the CNC changes to error state.
The monitoring status is modal and remains active even after NC program end or RESET.
Syntax of Monitoring specific clamped axes: |
#CLAMP MONITORING ON | OFF [ { AX=<axis_name> | AXNR=.. } ] |
AX=<axis_name> | Name of clamped axis to be monitored. |
AXNR=.. | Logical number of the axis to be monitored, positive integer |
Syntax of Monitoring all clamped axes: |
#CLAMP MONITORING ON | OFF ALL |
Programing Example
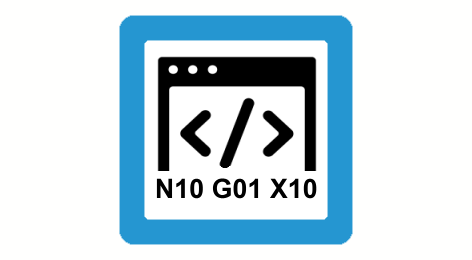
Axis clamping and monitoring
%clamp.nc
N010 X0 Y0 Z0 A0 B0 C0
N020 A[M300] C[M300] ;mechanical clamping of axes A+C on
N030 #CLAMP MONITORING ON ALL ;monitoring axes A+C on
..
N100 #CLAMP MONITORING OFF ALL ;monitoring axes A+C off
..
N110 #CLAMP MONITORING ON [AX=A AX=C] ;monitoring A+C on
N120 Y10
N130 X15
N140 #CLAMP MONITORING OFF [AX=A AX=C] ;monitoring A+C off
N150 X10
N160 #CLAMP MONITORING ON [AXNR=4 AXNR=6] ;monitoring axes A+C on
N120 Y20
N130 X25
N150 A[M301] C[M301] ;release mechanical clamping axes A+C
N140 #CLAMP MONITORING OFF [AXNR=4 AXNR=6] ;monitoring axes A+C off
..
N999 M30
Notice
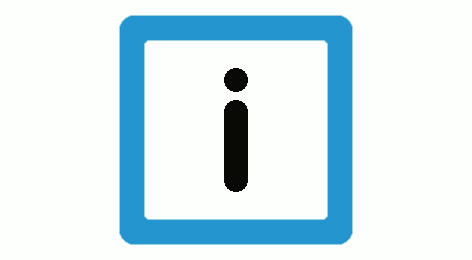
The command does not cause any mechanical axis clamping. Instead, it enables the monitor for unauthorised axis motions. With the function ‘Backward motion on path’, the monitor status is inverted accordingly.
Notice
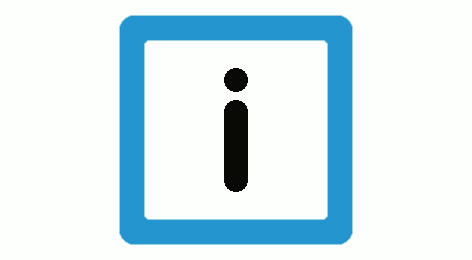
Axis motions which are generated by active compensation functions in the axis driver (e.g. Cross compensation, Volumetric Compensation, etc.) are not monitored.
The monitoring status of an axis can be read by the ADS access.
Index group: 0x20300
Index offset: 0x10189 (axis 1)
.