Process
To ensure that the cycle is executed successfully, the following requirements must be met.
- The tool radius is defined by V.G.WZ_AKT.R
- Tool length compensation is active.
- The spindle speed must be selected before the cycle is started.
- The start point in the XY plane (see below) can be reached without collision starting from the current position at the height of the retraction plane.
- A maximum of 3 systems may be active or defined when the cycle is called to ensure that sufficient machining coordinate systems (#CS) are available for the cycle.
Within the cycle, the tool is fed incrementally along the Z axis. The starting point here is a start point which has a safety clearance to the blank set by @P13 in the XY plane and is vertically parallel to the Y axis above the spigot centre. The blank is repeatedly approached in a circular movement for each machining height. With a clockwise machining direction (@P30=0), approach is counter-clockwise and departure is clockwise. With a counter-clockwise machining direction (@P30=1), approach is clockwise and departure is counter-clockwise.
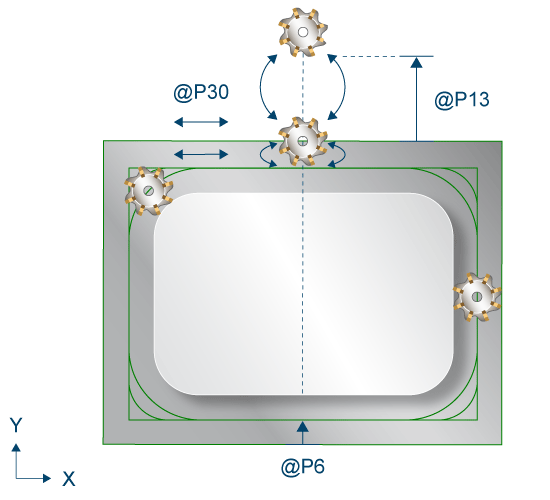
Roughing process
At the start, the start point in the XY plane is approached at the height of the retraction plane. The first feed is to the safety plane at rapid traverse along the Z axis followed by a feed to the machining height at the feed rate defined by @P21. Starting at this start point, an iterative feed takes place at the new machining height until the spigot depth @P4 is reached with the addition of the finishing allowance at the base (@P15). The maximum infeed per pass is the maximum infeed in Z at the maximum value defined in @P5.
The blank is first milled linearly for every machining height, i.e. without considering the corner radius (@P65). The tool then approaches closer to the centre of the spigot in a circular movement each circumferential pass without exceeding the maximum feed in XY (@P6). Linear removal continues until the linear outer dimensions of the spigot (@P72 and @P73) with the addition of the finishing allowance at the edge (@P16) are removed.
When linear machining is completed, the corner radius is milled (@P65). Corner removal continues every circumferential pass around the spigot until the correct radius (corner radius + finishing allowance in XY) is reached.
To avoid jerky movements in the milling path and thus relieve the machine tool, it may be useful to activate polynomial smoothing during roughing. This also leads to an accelerated execution of the milling cycle. The parameterisation of polynomial smoothing should be made dependent on the selected finishing allowance in order to avoid damage to the outer contour. To avoid residue, the maximum infeed in XY must then be reduced.
The milling cycle with polynomial smoothing can be called as follows:
#CONTOUR MODE [DEV, PATH_DEV = V.G.WZ_AKT.R / 10 ] ( Parameterisation )
G261 ( Activation of polynomial contouring )
L CYCLE [NAME = SysMill... ] ( Roughing )
G260 ( Deactivation of polynomial contouring )
L CYCLE [NAME = SysMill... ] ( Finishing )
M30
Finishing process
The start point mentioned for roughing is also approached as the starting position for finishing. From there, an interative feed takes place up to the new machining height until the spigot depth @P4 is reached. The maximum infeed per pass is the maximum infeed in Z at the maximum value defined in @P5.
A distinction is made between two cases for the milling operation at each machining height:
- If no finishing allowance at the base needs to be removed at the current machining height, only the finishing allowance around the spigot is removed. As for roughing, linear removal first takes place (as required) before the correct corner radius is removed.
- If the current machining height also involves a removal of the finishing allowance at the base, the complete blank must be again machined at this height until the correct spigot dimensions are reached. Here too, removal is first linear before the corner radius is removed.