Programming example
Programing Example
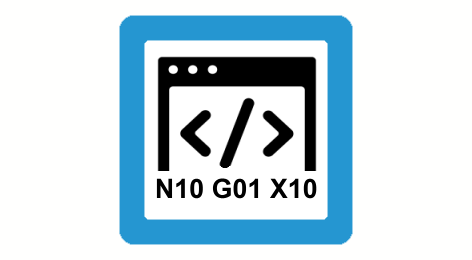
Multi-edge milling
T8 D8 ( Tool data )
M6 ( Tool change )
G90 G54 S6000 M03 F2000 ( Technology data )
#VAR
; input parameters:
V.L.SurfacePosition = 0 ( Z position of workpiece surface )
V.L.RetractionPlane = 50 ( Z position of retraction plane )
V.L.SafetyClearance = 2 ( relative value of safety clearance in Z )
V.L.Depth = 5 ( depth of multiedge )
V.L.MaxIncrementZ = V.L.Depth ( maximum infeed in Z )
V.L.MaxIncrementXY = V.G.WZ_AKT.R ( maximum infeed in XY )
V.L.FeedRateXY = 6000 ( machining feedrate in XY )
V.L.FeedRateZ = 4000 ( plunging feedrate )
V.L.NumberOfEdges = 6 ( number of edges )
V.L.BlankRadius = 25 ( radius of the blank )
V.L.EdgeLength = 10 ( length of the edges )
#ENDVAR
G00 Z60 ( Go to Z start position )
G00 X25 Y25 ( Go to centre of the multi edge )
; polynomial contouring for smooth movements
#CONTOUR MODE [DEV, PATH_DEV = V.G.WZ_AKT.R / 100]
G261
L CYCLE [NAME=SysMillMultiEdge.ecy \
@P1 = V.L.SurfacePosition \
@P2 = V.L.RetractionPlane \
@P3 = V.L.SafetyClearance \
@P4 = V.L.Depth \
@P5 = V.L.MaxIncrementZ \
@P6 = V.L.MaxIncrementXY \
@P20 = V.L.FeedRateXY \
@P21 = V.L.FeedRateZ \
@P31 = "Roughing" \
@P44 = V.L.NumberOfEdges \
@P71 = V.L.BlankRadius \
@P72 = V.L.EdgeLength \
]
G260
M05
M30