Introduction
Transformation types
The transformations listed below are 3, 4, 5 and 6-axis kinematic transformations. They are only required on machines with
- non-Cartesian axis arrangement or
- with rotary axes
to adjust orientation if programming takes place in the WCS (Workpiece Coordinate System). In general, this case results in non-linear equations that reflect the correlation between workpiece coordinates and machine coordinates.
Workpiece axes are axes that are located on the workpiece side in the kinematic chain. Tool axes are axes which are on the tool side.
A distinction is made between the following transformation types
- RTCP Transformation (Rotation Tool Centre Point): In this case, spatial positions are programmed in the WCS. The tool direction is set by programming the rotary machine axes (e.g. B and C are independent of the machine). Auxiliary functions permit automatic tool orientation to rotated coordinate systems in space.
- Example of NC program line: N10 X100 Y20 Z30 B0 C0
- Complete transformation: In this case, spatial curves and the tool machining orientation are programmed by position and orientation (point-vector sequences) and are always independent of the machine type with 6 coordinates (*).
- Example of NC program line: N10 X100 Y20 Z30 A0 B0 C1
(*) Depending on the degrees of freedom of a kinematic feature, only the position may be programmed by 3 coordinates (e. g. Tripod).
Notice
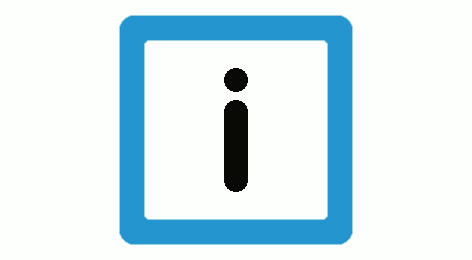
Transformations are additional options and subject to the purchase of a license.
Attention
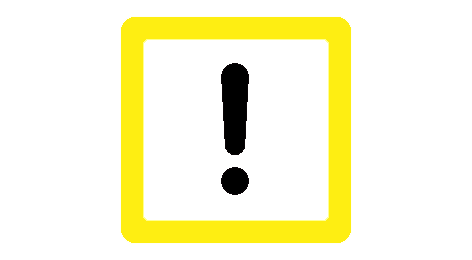
When kinematic transformation is active, axis-specific tool offsets in ax_versatz[<ax_index>] (P-TOOL-00006) are only taken into consideration if axes are not influenced by the transformation function. Depending on the transformation type, they typically refer to all axes with index > 2 when RTCP is used.
The axis-specific tool offsets of the first 3 axes (index 0, 1, 2) are not taken into account when transformation is active. If tool offsets should also be effective for these axes when transformation is active, enter the values in the kinematic offsets of the tool (P-TOOL-00009) mentioned above.
The necessary kinematic-specific axis configuration setting must be entered in the channel parameters.
It is essential to use the correct axis index sequence for the selected transformation.