KIN_TYP_45 – 6-axis articulated robot kinematics
Kinematic structure
Articulated robot with 6 machine axes. All articulated axes of the robot except for the manual axes A1 and A2 are linear axes. The axes A1 and A2 are modulo axes with ranges of 0 to 180, 0 to -180 degrees. The joint axis C1 can also be configured as a modulo axis if no trailing cable must be considered.
Axis configuration in the NC channel | ||
Axis identifier | X, Y, Z, A, B, C (C1, B1, B2, A1, B3, A2) | |
Axis index | 0, 1, 2, 3, 4, 5 | |
Kinematic structure | ||
| Tool axes | Workpiece axes |
NC axes | X, Y, Z, A, B, C | - |
Offset data of kinematics
HD offset | param[i] | Description | Unit |
HD1 | 0 | Tool Z offset in the Flange Coordinate System (variant 1) | 1.0 E-4 mm |
HD2 | 1 | Tool X offset in the Flange Coordinate System (variant 1) | 1.0 E-4 mm |
HD3 | 2 | Tool Y offset in the Flange Coordinate System (variant 1) | 1.0 E-4 mm |
HD4 | 3 | Angle of tool rotation about the X'' axis | 1.0 E-4° |
HD5 | 4 | Angle of tool rotation about the Y'' axis | 1.0 E-4° |
HD6 | 5 | Angle of tool rotation about the Z axis | 1.0 E-4° |
HD7 | 6 | Z offset from origin of Cartesian spatial coordinate system to rotation point of joint axis 2 | 1.0 E-4 mm |
HD8 | 7 | Z offset from rotary axis joint 2 to rotary axis joint 3 | 1.0 E-4 mm |
HD9 | 8 | X offset from rotary axis joint 3 to rotary axis joint 5 | 1.0 E-4 mm |
HD10 | 9 | X offset from manual axis joint 5 to flange surface on joint 6 | 1.0 E-4 mm |
HD11 | 10 | X offset from origin of Cartesian spatial coordinate system to rotation point of joint axis 2 | 1.0 E-4 mm |
HD12 | 11 | Z offset from rotary axis joint 5 to rotary axis joint 3. Please refer to note under the table. | 1.0 E-4 mm |
HD14 | 13 | Rotary offset for zero position of robot joint axis 2 (see Angle offset) | 1.0 E-4° |
HD15 | 14 | Rotary offset for zero position of robot joint axis 3 (see Angle offset) | 1.0 E-4° |
HD21 | 20 | Rotation direction of joint axis 1: 0 (positive), 1 (negative) | [ - ] |
HD22 | 21 | Rotation direction of joint axis 2: 0 (positive), 1 (negative) | [ - ] |
HD23 | 22 | Rotation direction of joint axis 3: 0 (positive), 1 (negative) | [ - ] |
HD24 | 23 | Rotation direction of joint axis 4: 0 (positive), 1 (negative) | [ - ] |
HD25 | 24 | Rotation direction of joint axis 5: 0 (positive), 1 (negative) | [ - ] |
HD26 | 25 | Rotation direction of joint axis 6: 0 (positive), 1 (negative) | [ - ] |
HD31 | 30 | Flange Coordinate System: | [ - ] |
HD32 | 31 | Y offset from rotary axis joint 4 to rotary axis joint 1. Please refer to note under the table. | 1.0 E-4 mm |
HD33 | 32 | Control flag for machining type 0: Default Once you set the parameter HD33, the machining mode switches to the mode of the moved workpiece. We therefore advise you to set this parameter first by selecting the fixed tool and positioning the robot in readiness or to set this parameter in the tool management system. | [ - ] |
HD34 | 33 | Tool length compensation direction 0: none (default) By default, the entered tool length is not included when you select a tool with Kinematic 45 enabled. If this parameter is unequal to 0, the tool length is included in the set direction. | [ - ] |
HD35 | 34 | Rotation sequence of tool orientation HD4-6 0: Z Y’ X‘‘ (default) | [ - ] |
HD36 | 35 | Rotary offset for zero position of robot joint axis 1 | 1.0 E-4° |
HD37 | 36 | Rotary offset for zero position of robot joint axis 4 | 1.0 E-4° |
HD38 | 37 | Rotary offset for zero position of robot joint axis 5 | 1.0 E-4° |
HD39 | 38 | Rotary offset for zero position of robot joint axis 6 | 1.0 E-4° |
Notice
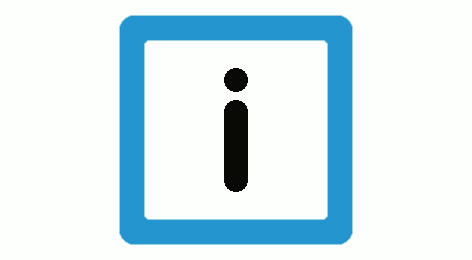
Set the correct sign for parameters HD12 and HD32.
HD12: Positive sign; the rotary axis of joint 3 is located in the positive Z direction above the rotary axis of joint 5
HD32: Positive sign; the rotary axis of joint 1 is located in the positive Y direction above the rotary axis of joint 4
Robot poses can also be specified as an alternative to axis-specific positioning, see [PROG// Status & Turn (IS, IT)].
For more information on kinematic offset data, see [CMS-A2].