Status & Turn (IS, IT)
An option exists to specify the robot pose for the corresponding Cartesian position as an alternative to axis-specific positioning and to obtain a more precise specified position of a #PTP movement for industrial robots.
The robot pose is therefore described using Status (IS).
In addition, the signs of the axis positions are described using Turn (ÍT)
It is not permitted to program Turn without Status.
Notice
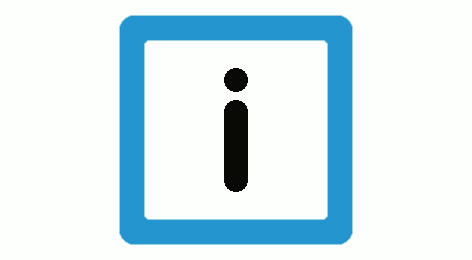
Robot positioning with Status & Turn is currently only available for kinematic type 45.
Status bit
An overview of robot poses is contained in Kinematic poses of six-axis articulated robot.
The robot pose is divided into 3 criteria. If a criterion applies, a corresponding numerical value is added to the status.
1st criterion If the wrist is behind axis A1, decimal 1 or binary 1 is added (yellow area in the figure on the left).
2nd criterion If the wrist is in front of the straight line through axes A2 and A3, decimal 2 or binary 10 is added (centre and right image).
3rd criterion Indicates the position of axis A5. If A5 < 0, decimal 4 or binary 100 is added.
Turn bit (optional)
The optional turn value lists the negative signs of the axis angles.
When the turn value is considered in a binary representation, the sign of each axis angle is assigned to a bit. These are then added to a number, i.e. the turn.
If the axis angle of an axis is < 0°, the value is 1.
| A6 < 0° | A5 < 0° | A4 < 0° | A3 < 0° | A2 < 0° | A1 < 0° |
Binary | 100000 | 010000 | 001000 | 000100 | 000010 | 000001 |
Decimal | 32 | 16 | 8 | 4 | 2 | 1 |
If all 6 axis angles are in the negative range, this results in a turn value of decimal 63 or binary 111111; accordingly, this results in decimal 0 and binary 000000 for 6 positive axis angles.
Notice
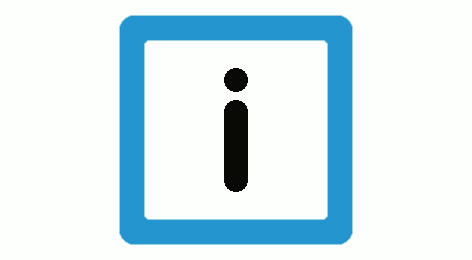
The turn value must be consistent with the status value.
For example, a 1 in status bit 2 describes a negative A5 angle. In addition, if the A4 turn bit is set to 0 (positive A5 angle), the status and turn values are in contradiction. In this case, an error message is output.
Description
The additional parameters Status & Turn are available for unambiguous programming of the robot poses (Kin_Typ_45) with Cartesian target coordinates of a PTP movement.
Syntax of Programming Status & Turn with the prefixes “IS” and “IT” (optional): |
#PTP ON G.. X.. Y.. … IS.. IT.. #PTP OFF |
Binary numbers can be programmed with the following syntax:
'B<0…1>', or '2#<0…1>', or '02#<0…1>'.
When binary numbers are used, the syntax is as follows:
Status: IS'Bxxx'
Turn: IT'Bxxxxxx'
When decimal numbers are used, the syntax is as follows:
Status: IS<expr>
Turn: IT<expr>
Display values
The following CNC objects are provided for this function:
- mc_st_valid_r: Validity of the status & turn value
(Task COM index group 0x12010<CID> Index offset 0xB1) - mc_st_status_r: Status value of kinematic 45
(Task COM index group 0x12010<CID> Index offset 0xB2) - mc_st_turn_r: Turn value of kinematic 45
(Task COM index group 0x12010<CID> Index offset 0xB3)
Notice
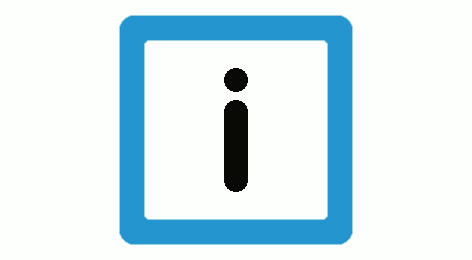
If Status & Turn are not programmed, the target point is determined on the axis angle level using the shortest way strategy.
Programing Example
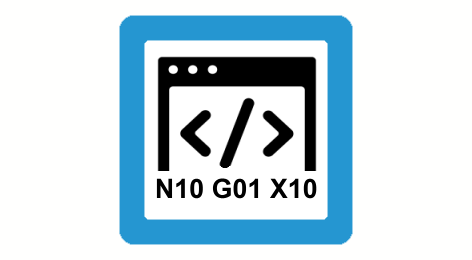
Status & Turn programmed with binary numbers
N010 #PTP ON
N020 G01 X1100 Y0 Z1400 A0 B90 C0 IS'B010' IT'B000010' F5000
N030 G01 X1200 ;target point is determined by shortest way
N040 #PTP OFF
Programing Example
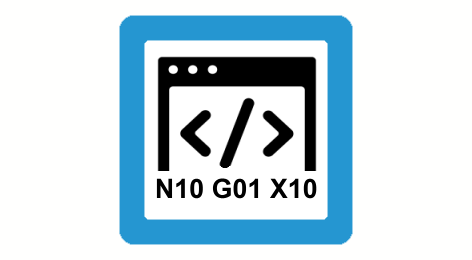
Status & Turn programmed with decimal numbers
N010 #PTP ON
N020 G01 X1000 Y0 Z1400 A0 B90 C0 IS2 IT2 F5000
N030 #PTP OFF
N040 G01 X1500
N050 G01 Y1000
N060 G01 X-1000
N070 #PTP ON
N080 G01 X-1000 Y-1000 ;target point is determined by shortest way
N090 #PTP OFF