Standard turning functions
Standard turning functions are used for conventional turning work with an endlessly rotating spindle. A position-controlled interpolated CNC spindle axis must be configured as the main spindle to achieve the full scope of functions. For details see [FCT-S1].
The tool-carrying spindle axis is commanded at the assigned speed by the spindle commands M03, M04 and M05.
A longitudinal and a face turning axis must be identified by an entry in the axis parameter P-AXIS-00015. The figure above shows an example where the Z axis is marked as the longitudinal turning axis (bit 0x80) and the X axis as the face turning axis (bit 0x40).
The conventional axis configuration consists of 3 Cartesian main axes in the order X-Y-Z (1st main axis, 2nd main axis, 3rd main axis). Machining is executed in the programmed G18 plane (Z, X).
Notice
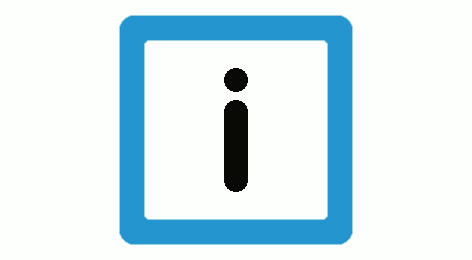
Recommendation: Configuration of the main axes X-Y-Z and machining in the G18 plane.
Machining can also be executed in the default G17 plane. The alternative axis configuration must then be Z-X-Y.
Standard turning functions
Function | Meaning | Unit |
G51 | Diameter programming | - |
G52 | Deselection of diameter programming | - |
G41, G42 | Tool tip radius compensation, left/right | - |
G40 | Deselect tool tip compensation | - |
G95 | Feed rate per revolution | F [mm/rev] |
G33 | Thread cutting | K [mm/rev] |
G96 | Constant cutting speed | S [m/min] |
G196 | Max. speed for G96 | S [rpm] |
G94 | Default unit for path feed | F [mm/min] |
G97 | Default unit for spindle speed | S [rpm] |
F: Path feed S: Spindle speed, cutting speed K: Pitch |
Additional information
- Diameter programming (G51/G52)
- Cutter radius compensation (G40/G41/G42)
- 2D cutter radius compensation (CRC) and 5-axis kinematics
- Feedrate per revolution (G95 / G94)
- Thread cutting with endlessly rotating spindle (G33)
- Thread cutting at actual spindle speed
- Thread chain
- Constant cutting speed (G96/G97/G196)
- Constant cutting speed at feedrate per revolution (G96, G95)
- Tapping (G331/ G332)
- Thread drilling without compensating chuck (G63)
- Thread tapping with spindle actual positions
- Settings for turning functions (# TURN)