Description
Activation
When the function is activated, a CNC status signal is generated according to the control flag P-CHAN-00017 and signals a speed limit undershoot or the detection of a future speed limit undershoot.
Limit value
The speed limit is defined via the percentage weighting (P-CHAN-00089) of the F word in the NC program.
Advance, delay
The expected drop in velocity at block end can be signalled in advance by the parameter P-CHAN-00013. Accordingly, the signal can also be cleared with a delay by the parameter P-CHAN-00012. The parameters P-CHAN-00012 / P-CHAN-00013 can therefore define a type of hysteresis.
Distance, time
The parameter P-CHAN-00018 defines the zone parameter unit as either a distance or time.
The CNC generates the “speed limit detect” status signal if the path position is inside this zone.
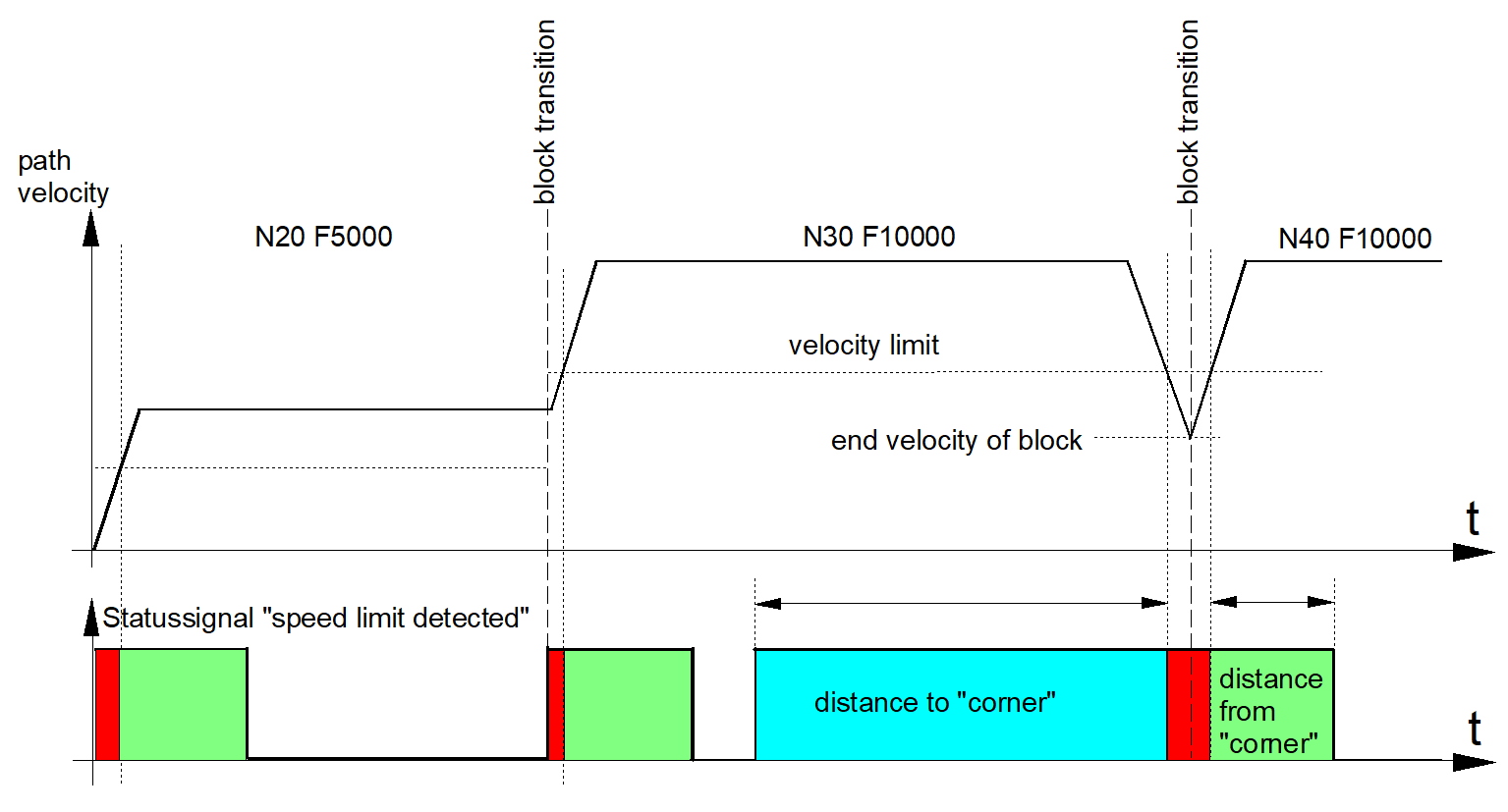
Influence of override
The parameter P-CHAN-00155 controls the influence of the speed limit by means of the real-time feed override.
In the default setting (P-CHAN-00155 = 0) the real-time
feed override does not influence the speed limit P-CHAN-00089. The “speed limit detect” status signal is also set if the path feedrate weighted by the override drops below the speed limit P-CHAN-00089.
Since override is a user-initiated online influence of speed, the delay/advance of the status signal cannot be evaluated in this case.
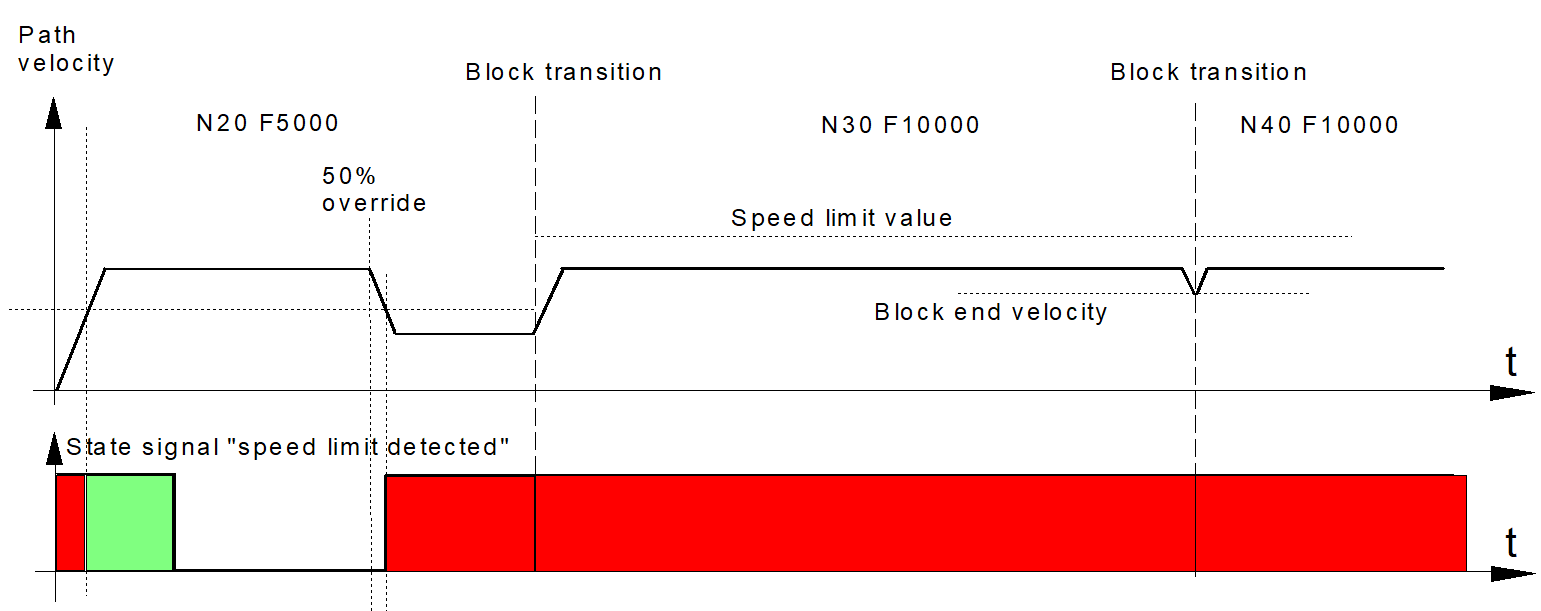
When P-CHAN-00155 is set, the parameterised speed limit P-CHAN-00089 is weighted by the override value. This is desirable e.g. for path start-up or run-in.
Note that, with a non-constant programmed feed, the "speed limit detect" signal is activated in each acceleration phase because the speed limit at the start of the block is set to the new value.
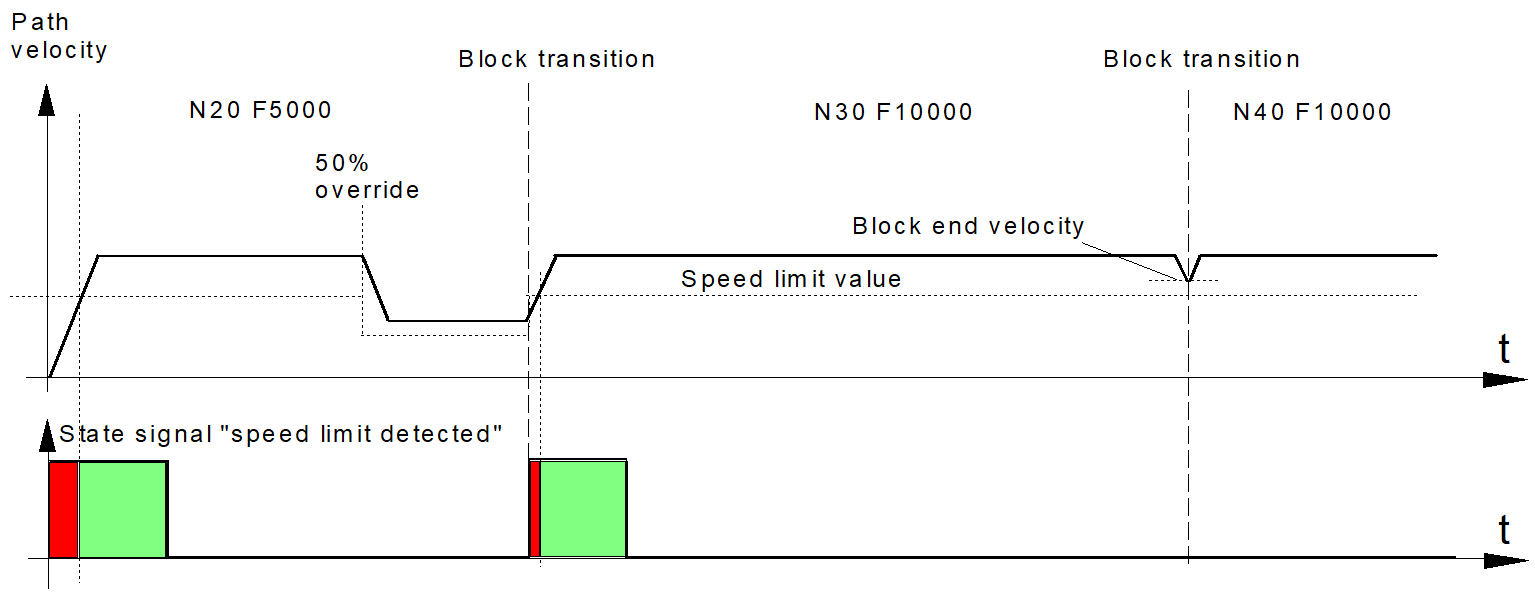
Influence of technology functions
The “speed limit detect” status signal is set if the CNC has to stop and wait due to certain types of technology functions or missing PLC synchronisation. In this case, the signal advance or delay related to the set time or distance is also evaluated.
Waiting for PLC acknowledgement
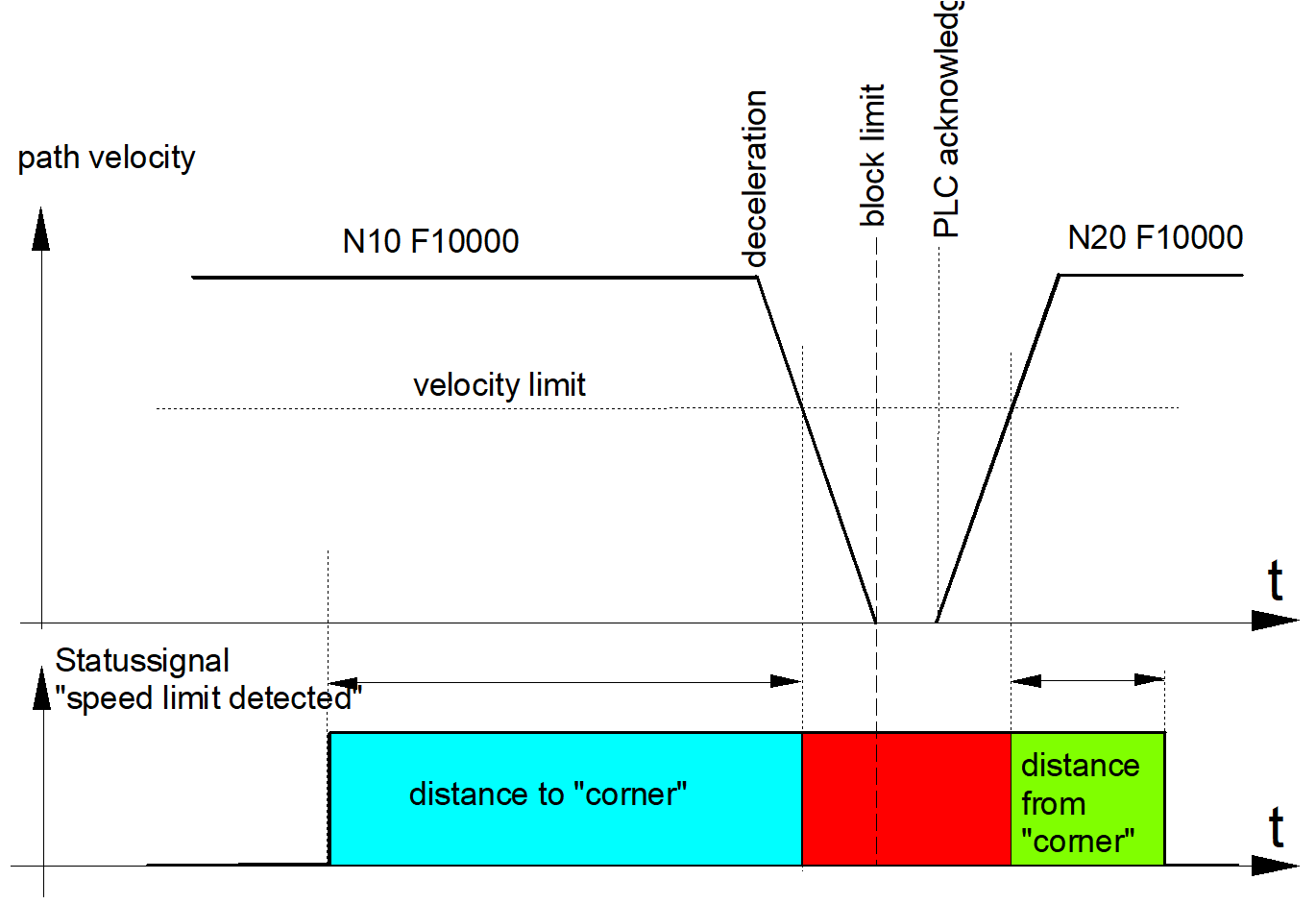
With M functions of the MVS_SNS type, later synchronisation or M functions with look-ahead are only stopped if the PLC acknowledgement is missing. If the PLC acknowledgement arrives before the motion, a restart can be executed immediately.
However, the advance signal (advance, distance to “corner”) can still be executed correctly although an actual speed undershoot no longer arrives.
PLC acknowledgement during deceleration
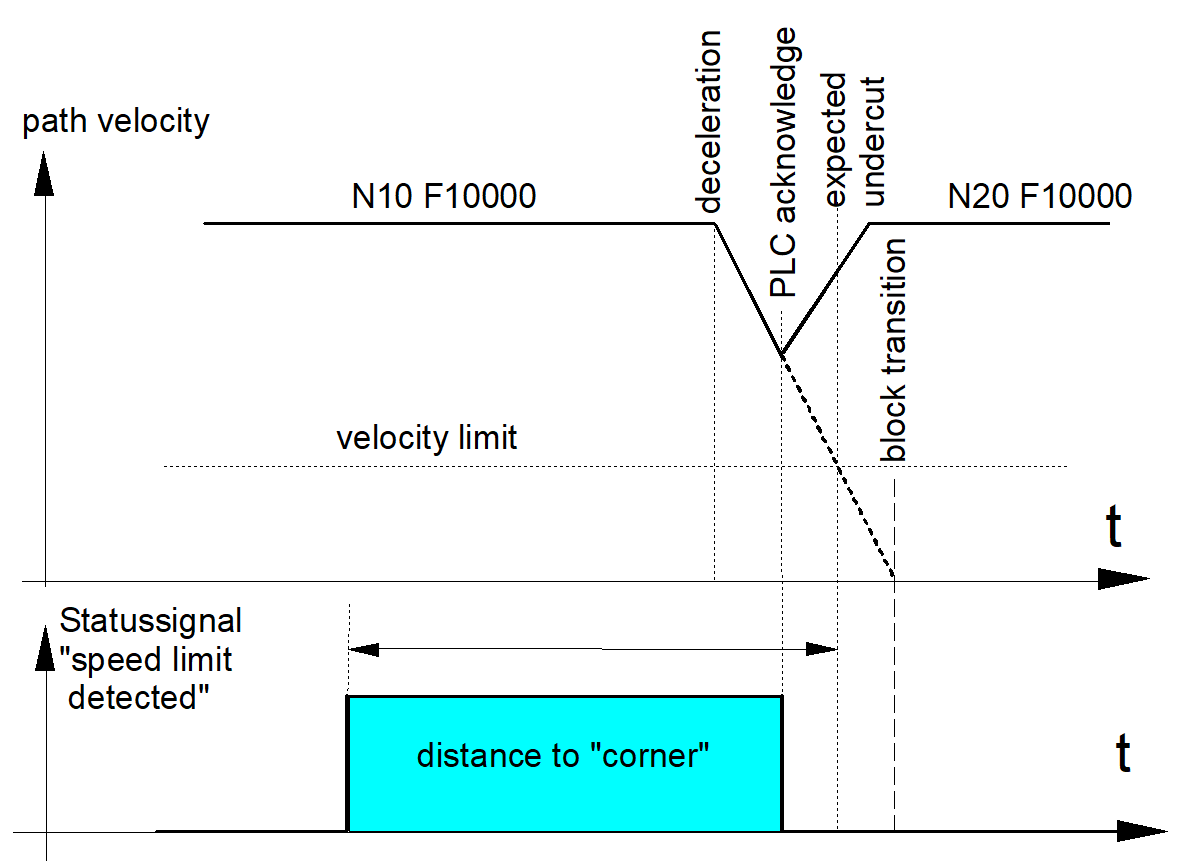
Notice
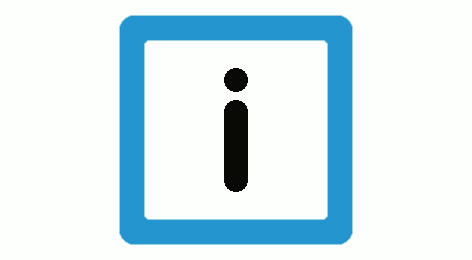
Each M or H function of the MVS_SVS or MNS_SNS type always results in a motion stop (see also [FCT-C1]).
Interruption of block supply
If the path velocity fluctuates due to short blocks and inadequate block supply, this may cause activation of the “speed limit detect” status signal. In the example below the advance/delay parameters (distance to corner and distance from corner) are disabled for the sake of simplification.
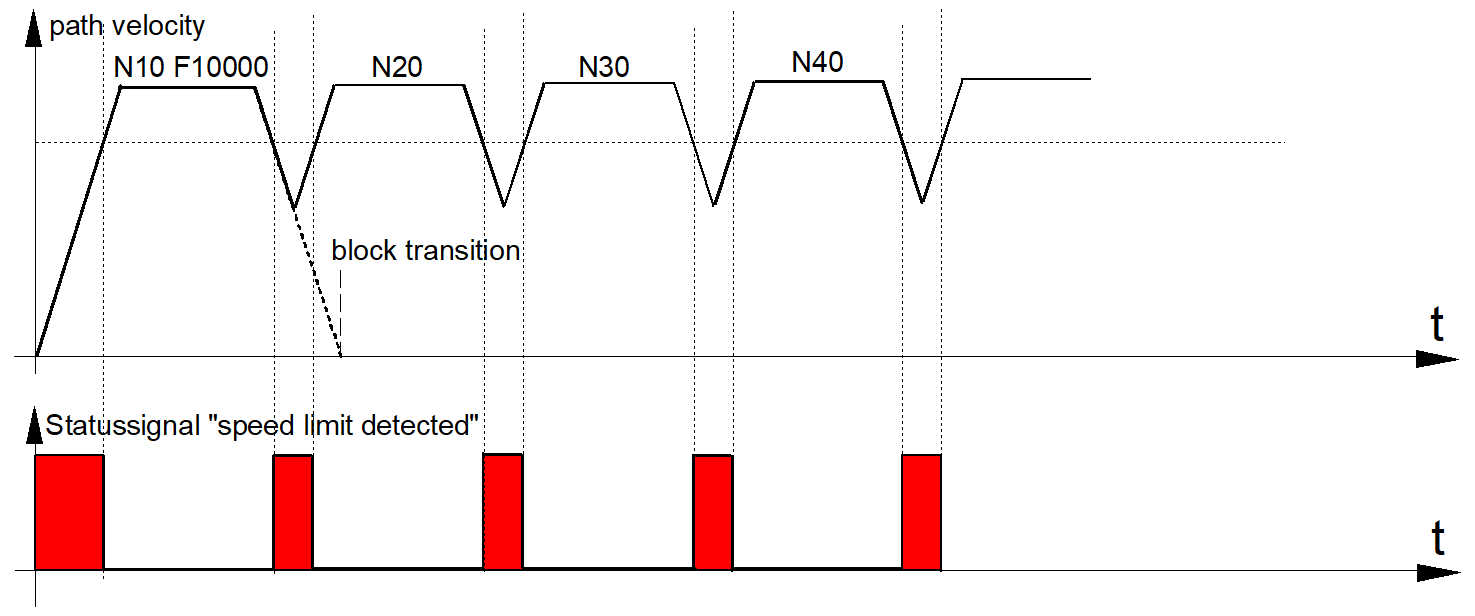