Programming software limit switch monitoring (POS_LIMIT)
The default setting of the software limit switches (SLS) is configured in the axis-specific lists by the parameters P-AXIS-00177 and P-AXIS-00178. After controller start-up, these limits are monitored for translatory axes and for every rotary non-modulo axis. The effectiveness of the monitoring function can be switched on and off for each axis by setting P-AXIS-00705 irrespective of axis type and axis mode. With modulo axes, the limits are only efrfective if they are located within the modulo range.
These default settings can be changed by NC command.
Syntax: |
<axis_name> [ POS_LIMIT ON | OFF | DEFAULT [ MIN=.. MAX=.. ] [BEHAVIOUR=<error_mode>] { \ } ] |
<axis_name> | Name of the axis |
POS_LIMIT | Identifier for the axis-specific programming of the software limit switch monitoring function. Must always be programmed as the first keyword. |
ON | Select software limit switch monitoring with new limits. MIN, MAX are optional; if not programmed, the previous limits remain valid. |
OFF | Deselect software limit switch monitoring |
DEFAULT | Reset the configured default values as per P-AXIS-00177, P-AXIS-00178 and P-AXIS-00705 |
MIN=.. | Lower limit switch limit in [mm, inch, °] |
MAX=.. | Upper limit switch limit in [mm, inch, °] |
BEHAVIOUR | Define the error response if the software limit switch is crossed: ERROR: Crossing results with an error already in path preparation (command value monitoring) ERROR_LR: Crossing results in a warning during path preparation. If crossing takes place, an error is output in the position controller (actual value monitoring). WARNING: If crossing takes place, only warnings are output in path preparation and in the position controller. |
\ | Separator ("backslash") for clear programming of the command over multiple lines. |
Notice
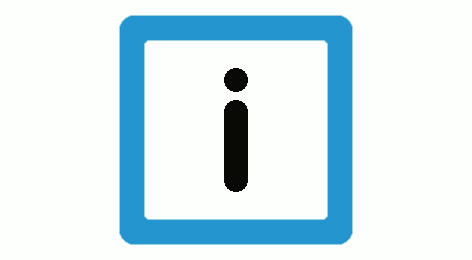
The software limit switches are checked in the axis coordinate system. The CNC channel checks the command positions, while the position controller checks the actual positions.
Notice
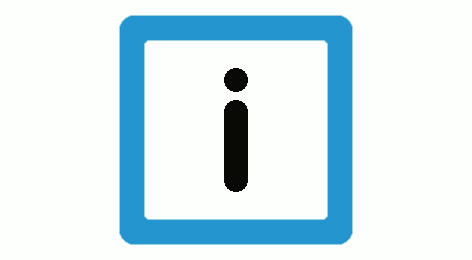
The configured limits P-AXIS-00177 and P-AXIS-00178 are not changed by this command. The limit switch limit values are reset to the configured default values at CNC reset, program start and axis exchange (e.g. #CALL AX). The change to the limit switch limit values when axis lists are re-read is considered at the next program start.
Programing Example
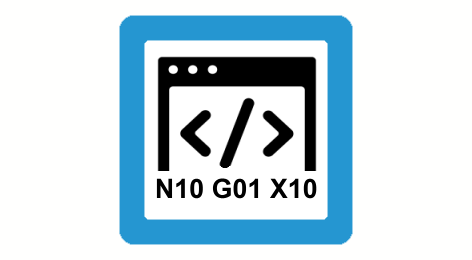
Programming of software limit switch monitoring
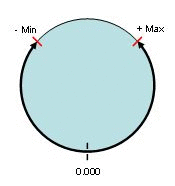
%pos_limit
:
;Select SLS monitoring:
N100 A[POS_LIMIT ON MIN=-135 MAX=135 BEHAVIOUR=WARNING]
:
;Select configured default values:
N200 A[POS_LIMIT DEFAULT]
:
;Deselect SLS monitoring:
N300 A[POS_LIMIT OFF]
:
M30