Drives with position control in the CNC
Notice
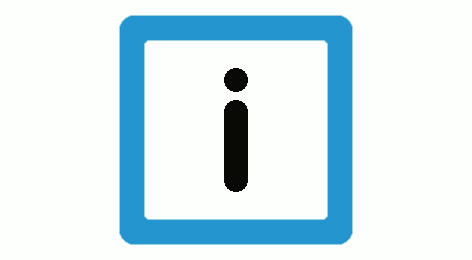
To change between position and speed control in CNC-controlled drives, the scaling of the manipulated variable (P-AXIS-00129, P-AXIS-00128) must be set correctly.
Parameterising the drive
For drives where position control is executed in the CNC, the drive must be in the ‘speed control’ operation mode. Otherwise, no special settings are required in the drive since a command speed is sent to the drive both in position-controlled and speed-controlled mode.
Settings in the CNC
For drives where position control can be executed both in the drive and in the CNC, e.g. with SERCOS, the operation mode “antr.operation_mode“ CNC-position control “CNC_POSITION_CONTROL” must be selected for the spindle (P-AXIS-00320).
To switch over to controlled mode, the scaling of the speed manipulated variable getriebe[i].multi_gain_z / getriebe[i].multi_gain_n (P-AXIS-00129, P-AXIS-00128, CMS-A1] must be set correctly. This can be checked by checking the displayed position lag at a constant endless motion M3 or M4 of the spindle and when feedforward control is inactive. When scaling is correct, the position lag value of the spindle speed caused by the proportional gain of the position control loop (see P-AXIS-00099) equals:
Position lag[°] = speed[°/s] / P-AXIS-00099 * 0.01[1/s]
The parameters antr.sercos.op_mode_for_velocity_control (P-AXIS-00264) for 'velocity control’ operation mode, antr.canopen.cyclic_position_op_mode (P-AXIS-00463), antr.canopen.cyclic_velocity_op_mode(P-AXIS-00464) and antr.sai_op_mode_change.feed_forward_v_weighting (P-AXIS-00766) have no meaning for CNC-controlled drives.