Beschreibung
Aufgabe
Die Überwachung kontrolliert, ob der aktuelle Schleppabstand den achsspezifischen Grenzwert überschreitet. Als Schleppabstand wird die Differenz zwischen Sollposition und rückgemeldeter Istposition bezeichnet.
∆s = ssoll - sist |
Die Überwachung jeder Achse erfolgt mit unterschiedlichen Grenzwerten im
- Stillstand und
- während der Bewegung.
Nach Auftreten eines Schleppfehlers wird der zugehörige Bahnverbund gestoppt.
Wenn nach einer Bewegung das istwertseitige Positionsfenster, P-AXIS-00236 (Genauhaltfenster, siehe Funktionsbeschreibung „Positionsüberwachung“, Kapitel Beschreibung [FCT-A3]) erreicht wird, dann schaltet die CNC für die Achse automatisch wieder auf Schleppabstandsüberwachung “Stillstand“.
Achtung
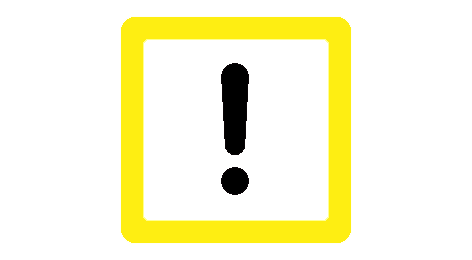
Die Verwendung der Schleppabstandsüberwachung entbindet den Inbetriebnehmer bzw. Betreiber der Maschine nicht von seiner Sorgfaltspflicht und der Anwendung von weiteren Überwachungsmaßnahmen wie z.B. der Geberüberwachung im Antriebsregler.
Voraussetzungen
Zur Verwendung der Schleppabstandsüberwachung muss die zu überwachende Achse in der Betriebsart 'Lageregelung' betrieben werden.
Die Lageregelung kann in der CNC oder im Antrieb stattfinden.
Für Achsen die nicht in der Betriebsart 'Lageregelung' betrieben werden, z.B. Spindeln, ist eine Schleppabstandsüberwachung nicht möglich.
Einschränkung
Eine konfigurierte Schleppabstandsüberwachung ist immer wirksam außer:
- Nachführbetrieb ist aktiv
- Messen auf Festanschlag ist aktiv
- Referenzieren auf Hardwareendschalter ist aktiv
Bei den obengenannten Funktionen wird die Schleppabstandsüberwachung vorübergehend deaktiviert und am Ende der jeweiligen Funktion wieder aktiviert.
Einsatzmöglichkeiten
Die Schleppabstandsüberwachung wird eingesetzt für:
- Antriebe, bei denen die CNC die Lageregelung übernimmt
- Antriebe, bei denen die Lageregelung im Antriebsregler durchgeführt wird
Hinweis
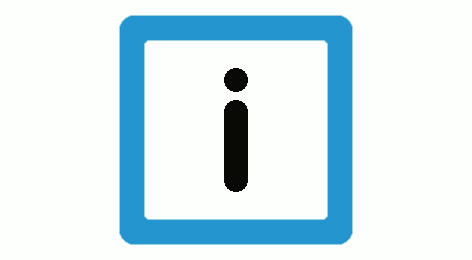
Bei Antrieben mit eigener Lageregelung sollte immer eine mögliche Schleppabstandsüberwachung des Antriebs genutzt werden.
Wenn der Antrieb keine eigene Schleppabstandsüberwachung durchführt, muss eine Überwachung durch die CNC erfolgen.
Aktivierung
Die Schleppabstandsüberwachung wird mit dem Parameter P-AXIS-00172 ein- oder ausgeschaltet.
VORSICHT
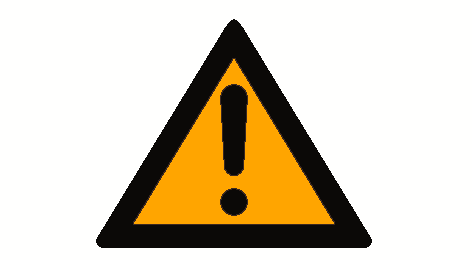
Personen- und Maschinenschaden möglich
Schleppabstandsüberwachung P-AXIS-00172 nicht deaktivieren, es kann zu einer Kollision der Achse kommen.
Warnungen, Fehler und Reaktionen
- Fehlermeldung P-ERR-70020: Der zulässige Schleppabstand wird bei bewegter Achse überschritten. Dies kann z.B. durch Kollision, schwergängige Führungen oder Überlast verursacht werden.
- Bei Lageregelung in der CNC: Öffnen des Lageregelkreises und stoppen der Achse über eine gesteuerte Nothaltrampe.
- Bei Lageregelung im Antrieb: Stoppen der Achse mit einer in der Achsparameterliste einstellbaren Verzögerung P-AXIS-00003.
- Anhalten aller Achsen, die mit der betroffenen Achse im Bahnverbund interpoliert werden.
- Ursache der Fehlermeldung prüfen und beheben
- Steuerung resetten
- Fehlermeldung P-ERR-70081: Der zulässige Schleppabstand wird bei stehender Achse überschritten. Dies kann z.B. durch äußere Krafteinwirkung auf die Mechanik oder durch Drift der Antriebsistposition verursacht werden.
- Sofortiger Stopp der betroffenen Achse.
- Anhalten aller Achsen, die mit der betroffenen Achse im Bahnverbund interpoliert werden.
- Ursache der Fehlermeldung prüfen und beheben
- Steuerung resetten
Hinweis
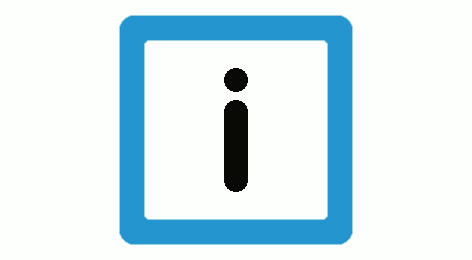
Weitere Maßnahmen können von der PLC über die Steuerschnittstelle vorgenommen werden.
Parametrierung
Die Schleppabstandsüberwachung wird mit P-AXIS-00172 für folgende Typen konfiguriert:
- Typ 0: keine Schleppabstandsüberwachung
- Typ 1: Standard Methode
- Typ 2: Lineare Methode
- Typ 3: Wird nicht mehr unterstützt!
- Typ 4: Geschwindigkeitsunabhängige Methode
Der zulässige Schleppabstand einer fahrenden Achse wird bei Typ 1 und 2 abhängig von der Sollgeschwindigkeit berechnet. Ebenso kann bei beiden Typen über ein Zeitglied der zulässige Schleppabstand zeitlich verschoben werden.
Der Standard Typ 1 verwendet einen parametrierbaren Filter.
Der lineare Typ 2 geht von dem theoretischen Schleppabstand bei konstanter Geschwindigkeit aus, der mit einem Faktor vergrößert werden kann.
Bei Typ 4 wird auch während einer Achsbewegung auf einen geschwindigkeitsunabhängigen konstanten Grenzwert geprüft.
Empfehlung für Typauswahl
Die Auswahl des geeigneten Typs hängt von den gegebenen Voraussetzungen ab. Empfehlung:
- Typ 1: Kv Faktor ist nicht bekannt
- Typ 2: Kv Faktor ist bekannt
- Typ 4: Die Achse wird mit Geschwindigkeitsvorsteuerung betrieben, unabhängig davon, ob die Regelung von der CNC oder im Antrieb durchgeführt wird.
Schleppabstandsüberwachung einstellen und kontrollieren
Schleppabstandsüberwachung während der Inbetriebnahme der Achse wie folgt einstellen und kontrollieren:
- Typ für die Schleppabstandsüberwachung auswählen und in P-AXIS-00172 eintragen.
- Fehlerausgabe der Schleppabstandsüberwachung durch Setzen von P-AXIS-00176 auf den Wert 1 unterdrücken. Es werden nun die durch den eingestellten Überwachungstyp festgelegten Grenzwerte berechnet.
- Testlauf mit Beobachtung der tatsächlichen Schleppabstandswerte sowie der berechneten Grenzwerte im Objektbrowser.
- Einstellen der Grenzwerte P-AXIS-00168 und P-AXIS-00169 unter Berücksichtigung von Reserven.
- Fehlerausgabe der Schleppabstandsüberwachung durch Setzen von P-AXIS-00176 auf den Wert 0 wieder freigeben.
VORSICHT
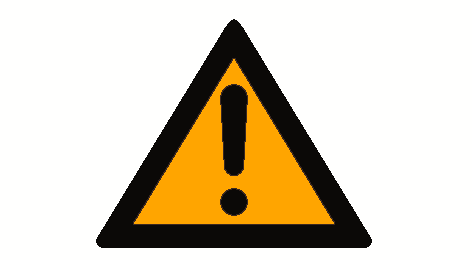
Personen- und Maschinenschäden möglich
Die Unterdrückung der Fehlerausgabe der Schleppabstandsüberwachung durch Setzen von P-AXIS-00176 auf den Wert 1 kann zu Personen- und Maschinenschäden führen.
Testablauf
Der empfohlene Testlauf besteht aus einer G1-Fahrt der Achse ohne Bearbeitung, aber mit der üblichen Last eines typischen Werkstücks auf der Maschine.
Der Verlauf des Schleppabstands kann mit dem ISG Objekt-Browser beobachtet werden.
Der Wert „absolute_position_lag“ zeigt den Betrag des Schleppabstandverlaufs im Test. Der konfigurierte maximal zulässige Wert P-AXIS-00168 kann unter „max.position_lag“ zum Vergleich angezeigt werden. Die Bestimmung von „max.position_lag“ ist abhängig von der verwendeten Methode.
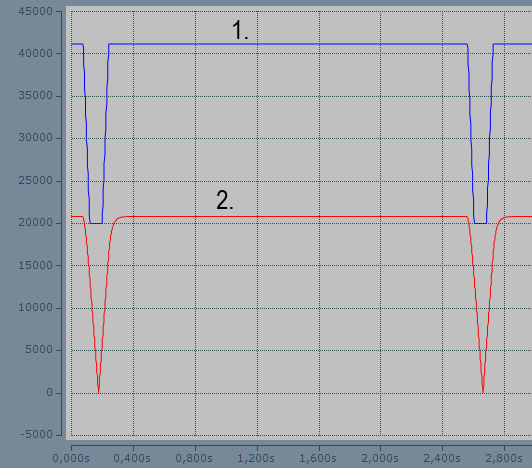
1. | absolute_position_lag: Absolutwert des Schleppfehlers |
2. | max.position_lag: Maximalwert des Schleppfehlers |
Kausales System, Systemlaufzeit
Der theoretische Schleppabstand ∆s hängt von der Sollgeschwindigkeit v und der wirksamen Lagereglerverstärkung kv wie folgt ab:
|
|
An der Achse ergibt sich jedoch ein realer Schleppabstandsverlauf, der eine Verzögerung zu dem Theoretischen aufweist. Diese Verzögerung wird verursacht durch:
- eine systembedingte Taktverschiebung im Lageregler der Steuerung sowie
- durch die mechanische Zeitkonstante des Systems.
Die Methoden zur Berechnung des zulässigen Schleppabstands berücksichtigen diesen Einfluss nicht. Deshalb muss mit einem zusätzlichen Zeitglied (PT1) der zulässige Schleppabstand verschoben werden.
- Zeitglied mit P-AXIS-00170 konfigurieren.
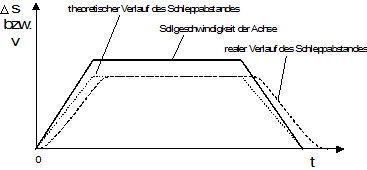
Laufzeit bei Antrieben mit eigener Lageregelung
Bei Antrieben mit eigener Lageregelung kann die CNC zusätzlich eine Überwachung des Schleppabstands durchführen.
Aufgrund der Laufzeit des Antriebsbusses und von Berechnungen im Antrieb selbst (Filterung, Feininterpolation) wird der von der Steuerung berechnete Lagesollwert erst mit einer Verzögerung von eventuell mehreren CNC-Takten wirksam.
Bei der Berechnung des Schleppabstands wird aber standardmäßig der zuletzt übertragene Sollwert und der aktuelle Istwert verwendet, sodass der berechnete Schleppabstand größer als der tatsächliche Schleppabstand ist.
Diese Verzögerung kann dadurch kompensiert werden, dass zur Schleppabstandsberechnung nicht der Sollwert des aktuellen Taktes, sondern ein älterer Sollwert verwendet wird. Durch den Parameter P-AXIS-00191 kann eingestellt werden, welcher der vergangenen Sollwerte zur Schleppabstandsberechnung verwendet werden soll.
Einstellung des Parameters
Zur Einstellung des Parameters P-AXIS-00191 wie folgt vorgehen:
- Lagereglerverstärkung (kv) aus dem Antriebsregler auslesen.
- Achse mit konstanter Geschwindigkeit bewegen und zugehörigen Schleppabstand berechnen mit:
- P-AXIS-00191 so einstellen, dass die Differenz zwischen dem steuerungsintern berechneten Schleppabstand und dem berechneten Schleppabstand minimal wird.
Im Allgemeinen ist es nicht möglich, eine exakte Übereinstimmung zwischen berechnetem und dem steuerungsintern berechneten Schleppabstand zu erreichen. Grund ist, dass die Zykluszeit des Antriebslagereglers kleiner ist als die Buszykluszeit, sodass die korrekte Verzögerung Bruchteile der Buszykluszeit beinhalten kann.
Alternativ kann der im Antriebsregler berechnete Schleppabstand in den zyklischen Prozessdaten zur Steuerung übertragen und dort anstelle des steuerungsintern berechneten Schleppabstands zur Überwachung verwendet werden. Siehe dazu folgender Abschnitt.
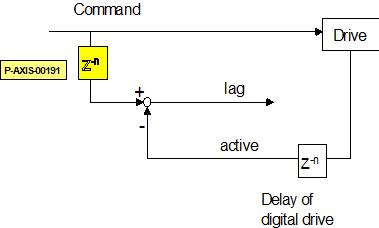
Verwendung des antriebsinternen Schleppabstands
Bei der Verwendung des antriebsintern berechneten Schleppabstands ist wie folgt vorzugehen:
- Konfiguration des Schleppabstands in den zyklischen Prozessdaten des Antriebs.
- Aktivierung der Auswertung des Antriebsschleppabstandes durch Setzen des Achsparameters P-AXIS-00466.